Overview: Optimizing new product design and appliance prototyping
FluidForming Americas (FFA) was approached by the world’s leading kitchen appliance manufacturer to help with the development of a high-performing kitchen appliance. We provided expert FEA analysis, part simulation, and appliance prototyping.
In this example, we’ll cover our collaborative process and the flexibility that’s possible with the FluidForming technology. We’ll even cover costs associated with the project.
Challenge: Finding optimal material and material thickness
Finding the optimal material and material thickness and then prototyping side, back, top, and bottom panels for three microwave oven cavity sizes.
Process & Solution: FluidForming hydroforming
The development and iteration process at FluidForming Americas was highly integrated with the manufacturer’s design team.
STEP 1: Finite Element Analysis
Upon receiving the purchase order and part drawings, FFA ran the design and material properties through a Finite Element Analysis (FEA). This crucial step helped ensure that components — and the specified materials and material thicknesses — would perform well during the FluidForming formation process.
STEP 2: Feedback
During the FEA simulation period, FluidForming’s engineering team provided regular feedback to the client’s appliance design team. This enabled the designers to make changes and improve the component before incurring tooling, material, and production costs. With each design variable change, FFA ran an FEA analysis until the design was approved by the client.
NOTE: If designers are unsure of what materials and material thicknesses will work best, FluidForming can provide the data they need — using FEA — to make informed decisions before prototyping or production begins.
STEP 3: Tooling
In this example, because the top and bottom parts were the same, a total of 11 tools were generated. Because FluidForming requires the use of a single tool and the prototyping tool can be used as the production tool, tooling costs are typically 50-90% lower than legacy die casting tooling expenses.
STEP 4: FluidForming Hydroforming
Part FluidForming was conducted on a FormBalancer 25 universal sheet metal and tube forming hydroforming press with a clamping force of 2,500 tons with a bed size of 800 mm x 800 mm with a maximum draw depth of up to 300 mm.
STEP 5: Iteration
When enamel testing showed that the back panel of the largest oven cavity wasn’t up to the client’s high standards, their designers made modifications to reinforce the panel and sent it back to FFA for FEA analysis and feedback. The existing tool was reworked and the parts were shipped on time, on budget, and on schedule.
Throughout the entire process, the FFA engineering team quickly responded to the client’s engineering, design, and testing needs on a tight timeline that included quick design iterations and FFA’s responsive production team enabled expedited prototyping.
Appliance Prototyping Cost Breakdown
FluidForming Costs
Tooling costs: $160,000. This includes forming simulation, engineering, consultation, tool design, materials, and tool creation of 11 different prototyping and production tools. (For a total of three different models)
Tooling reworking costs: $3,900. This includes simulation, consultation, tool redesign, tool re-cutting, and production.
Total cost per part: $80 per prototype.
Time to market: 16-18 weeks
Conventional Costs
Tooling costs: $390,000
Reworking costs: $73,000
Total Cost Per Part: $210
Time to Market: 18-28 weeks
NOTE: With FluidForming, quantity is not limited by tool search and the process can support marketing production and ramp-up production while permanent, high-volume tooling is created (as needed).
Because just one surface of the cavity’s sheet metal is exposed to the flexible and self-adjusting tool surface (water) under variably controlled pressures, the metal was forced evenly into the tool and onto the tool surface. Consequently, the finished parts were highly accurate parts and repeatable. FluidForming has a proven 99.996% first-pass yield rate.
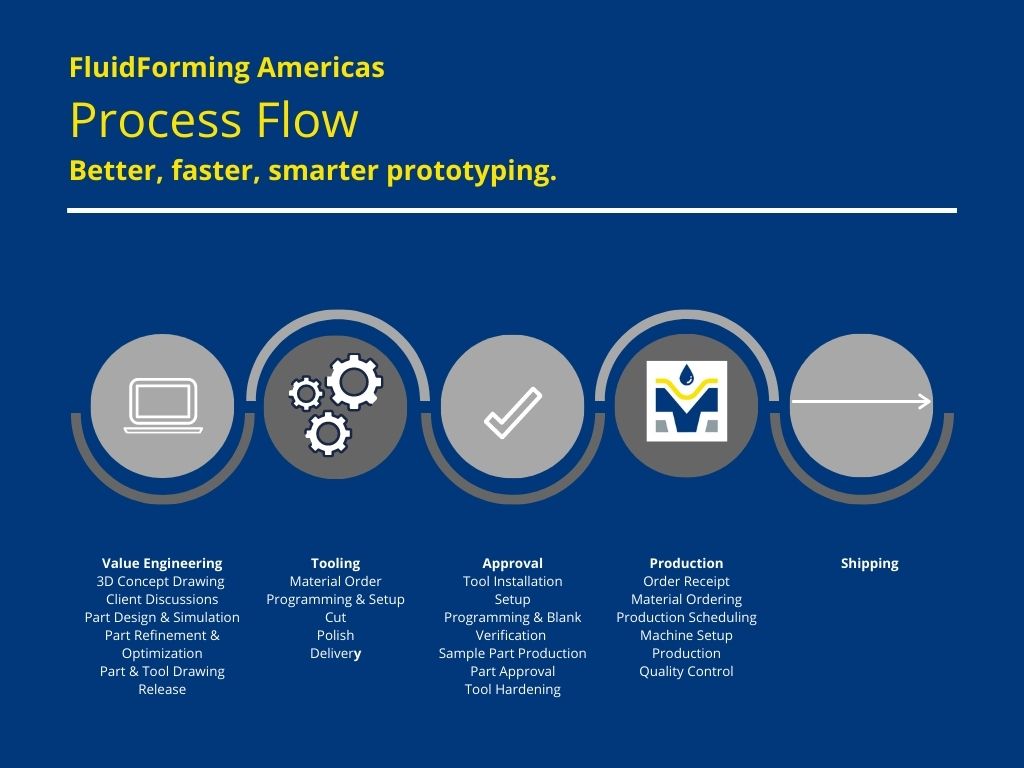
Summary: Created a significant market cost advantage, improved profit margins, reduced weight, improved performance, and lowered material costs
Discover how FluidForming enables innovation. To learn more about the FluidForming technology and process and to find out if our reinvention of hydroforming is right for your next project, contact FluidForming Americas at (800) 497-3545 or email us at info@ffamericas.com.