Metal Forming For Custom Furniture Makers
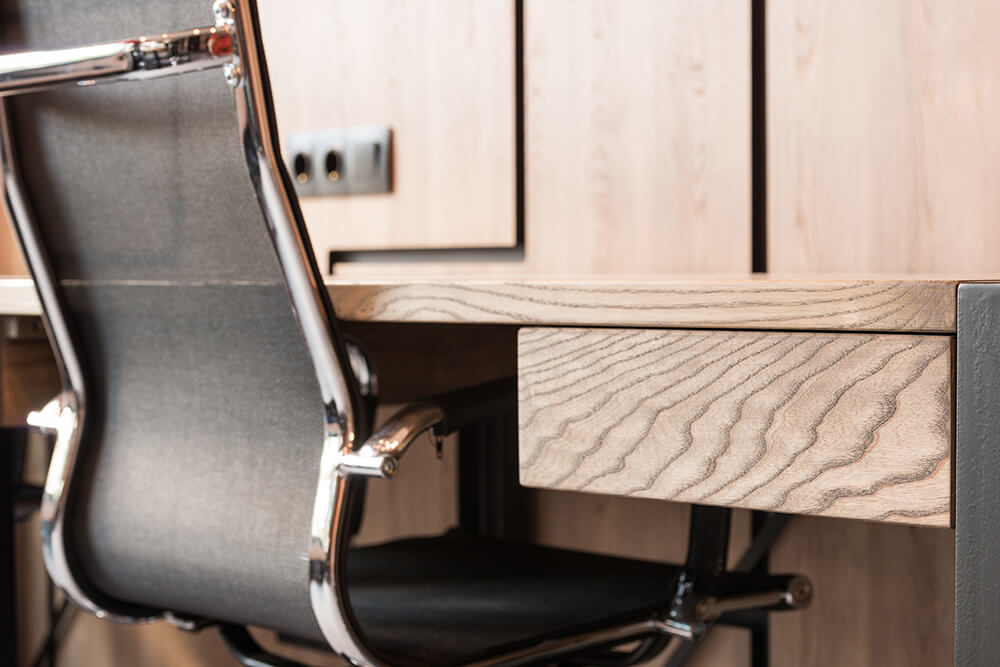
Precision sheet metal components for premium, sustainable furniture.
Whether you’re looking to create a singular, stunning piece of custom furniture or you need a larger production run, FluidForming hydroforming is the solution. Furniture manufacturers and designers enjoy the flexibility, lower overall production costs, and the clean look of FluidForming metal forming.
Our metal forming process is a revolutionary approach to legacy hydroforming. We enable rapid prototyping and same-day production of custom or limited-run furniture designs. Our universal sheet metal and tube forming machine, the FormBalancer, is a force-contained structure that permits extremely high forming pressures of up to 4,000 bar (60,000 psi). With up to 4x the forming pressure used by traditional hydroforming equipment, modern, highly-complex, and blemish-free furniture components can be sustainably formed with ease.
The new technology offers unparalleled furniture design flexibility and a greater strength-to-weight ratio than virtually any other metal forming process. Entire unibody pieces can be formed with our sheet metal or tube forming machine. We can also form individual legs, arms, adjustment tubes, armrests, brackets, table legs, portable chair and equipment bases, video monitor enclosures, and more.
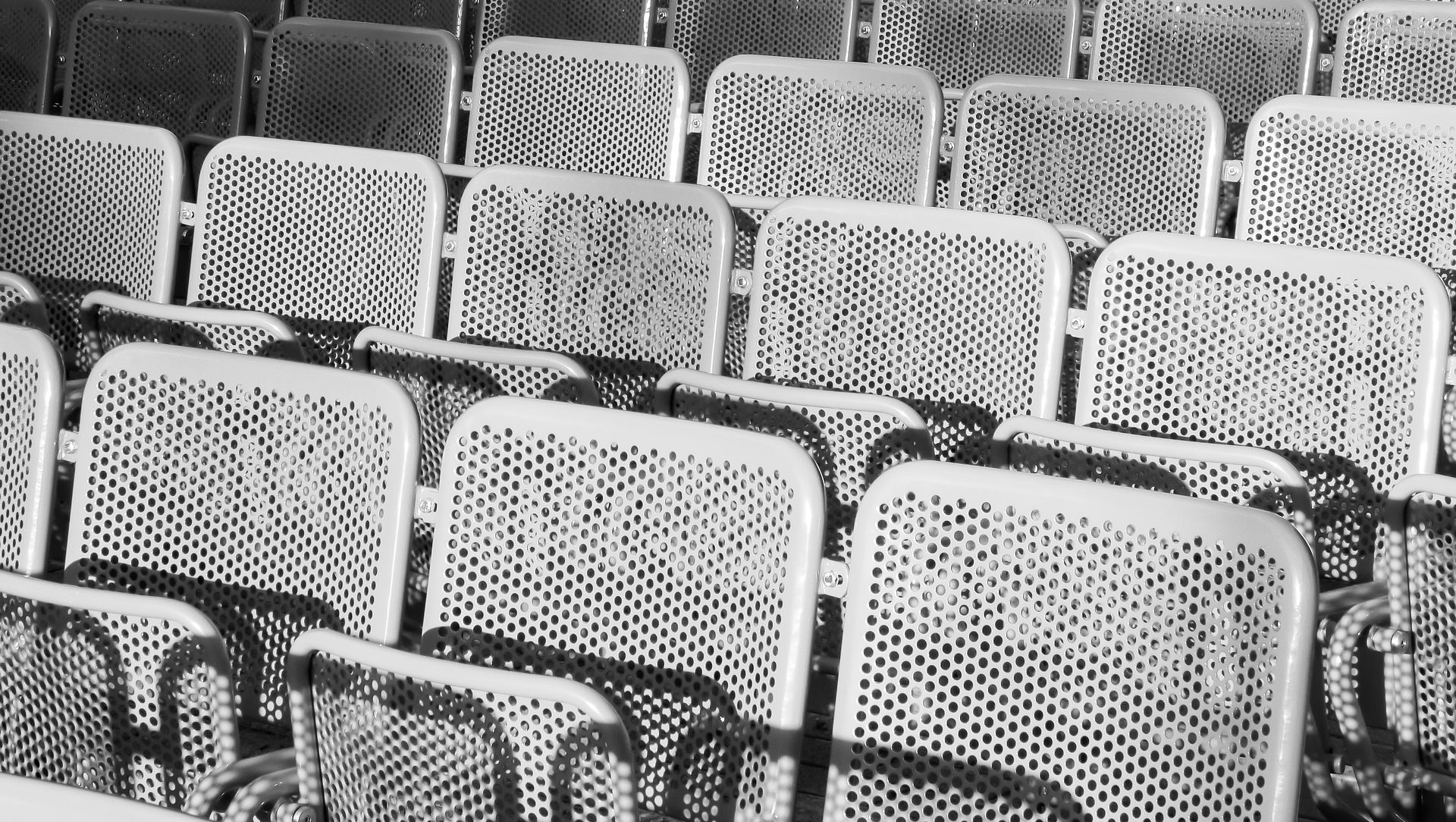
All-in-one metal forming technology.
FluidForming’s innovative approach to hydroforming offers a number of potential benefits for furniture designers and manufacturers.
Because the FormBalancer is the only universal hydroforming machine on the market, pressed sheet metal formed components and tubular shapes can be produced by a single machine. Additionally, tables, chairs, and bed frames produced using our metal forming process technology are lightweight, stable, and durable. Thanks to high forming pressures, advanced geometry and complex shapes can be readily achieved.
Unlike bladder-based systems, our bladder-free technology ensures the highest levels of surface quality and detail possible. Because pressurized water comes in contact with just one side of the metal surface, FluidForming is perfect for pre-finished materials. Trademarks, brands, monograms, and logos can all be easily incorporated into the design of each part.
Furniture designers enjoy the increased design flexibility that our fast prototyping capabilities enable. With FluidForming, designers are able to innovate and iterate seamlessly. Because our system accommodates the seamless transition from CAD to 3D-printed tooling, we’re able to move from design to production in a matter of days. Additionally, many individual parts can be incorporated into a single form, which can significantly reduce waste and overall production times.