Overview: Cast iron exhaust manifold replaced with stainless steel
Each year, the mass transit, commercial transportation, agricultural, recreational vehicle, and automotive industries develop, refine, and manufacture many millions of parts and components for vehicles each year. To meet demanding transportation industry safety regulations and fuel economy standards, these components must be durable, reliable, highly functional, and performance-driven.
Some parts that are commonly formed for these industries include protective enclosures, fuel cells, heat exchangers, body panels, battery enclosures, and exhaust manifolds.
In this case study, we’ll discuss how FluidForming made it possible for a lightweight stainless steel exhaust manifold to replace manifolds previous die cast from heavy and costly cast iron.
Problem: Cast iron manifolds too heavy and too costly
For years, our client had relied on die casting — a wasteful and environmentally harmful legacy method of metal forming — to produce exhaust manifolds for their performance snowmobiles. The foundry-made manifolds were heavy, expensive, and poorly made: they experienced a staggering 31% reworking rate.
Because FluidForming is the only Six Sigma metal forming process available to manufacturers, no two die cast parts were alike and each casting had to be cleaned, machined, and hand-welded.
Solution: FluidForming hydroforming
We replaced heavy and porous cast iron with smooth, lightweight stainless steel.
By dramatically reducing die, fixturing, and scrap costs and by eliminating reworking rates, our elegant and efficient solution made it possible for our client to accomplish two distinct goals: 1) develop a better product and 2) spend their newfound resources on research and development.
FluidForming is as committed to the environment as we are to innovation and accuracy, and our revolutionary process is inherently green. In stark contrast to conventional hydroforming, which relies on costly bladders and environmentally harmful hydraulic oil, or die casting which produces foundry waste and other harmful pollutants, the FluidForming technology relies solely on recycled tap water. Other environmental benefits include:
- Low energy consumption
- Low noise operation
- Overall material waste reduction
- Lower part weights
- Can replace environmentally harmful foundry cast or plastic parts with metal
- Rejected waste heat can be recovered and recycled
Results: Costs slashed and greater profits achieved
By turning to FluidForming, the company eliminated many downstream post-production steps (saving both time and money) and the manifold’s overall weight was reduced by more than 50%.
This dramatic weight reduction had the added benefit of reducing fuel consumption and improving performance. By using a high-quality stainless steel that could withstand high temperatures and was resistant to cracking, the manufacturer was able to develop an optimal exhaust flow pattern that improved the engine’s overall efficiency.
- Slashed die costs from $375,000 to less than $40,000 (88% savings)
- Reduced fixturing costs from $125,000 to less than $25,000 (80% savings)
- Eliminated post-production machining
- Reduced 30% scrap to 1%
- Reduced reworking rates from 31% to 0%
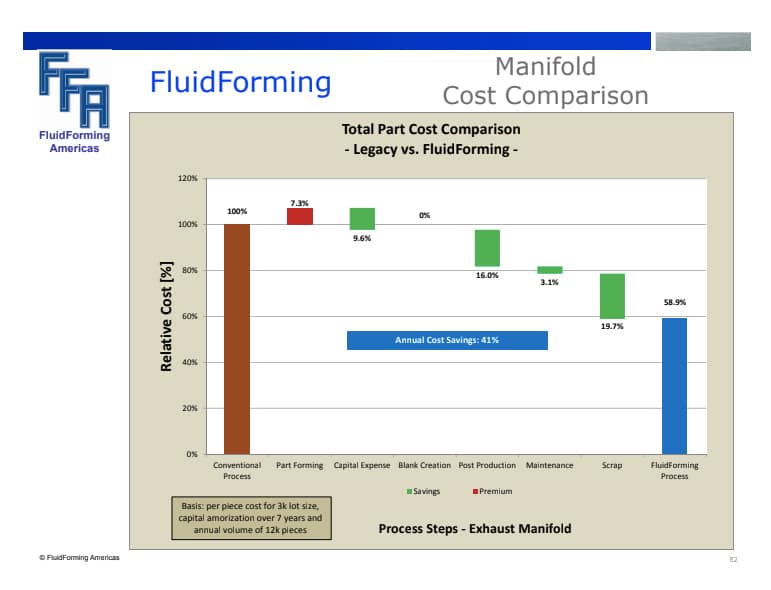
Summary: Created a significant market cost advantage, improved profit margins, reduced weight, reduced fuel consumption, improved engine performance, minimized environmental impact
Discover how FluidForming enables innovation. To learn more about the FluidForming technology and process and to find out if our reinvention of hydroforming is right for your next project, contact FluidForming Americas at (800) 497-3545 or email us at info@ffamericas.com.