Problem: Springback and significant downstream costs
For many years, this heat exchanger was formed using traditional die-stamping methods. The resulting parts experienced substantial springback, and because the two halves had to be welded together to form a complete unit, downstream costs for fixturing and clamping were significant. Die maintenance was expensive and reoccurring. All these inefficiencies resulted in lengthy production times and wasteful downtime.
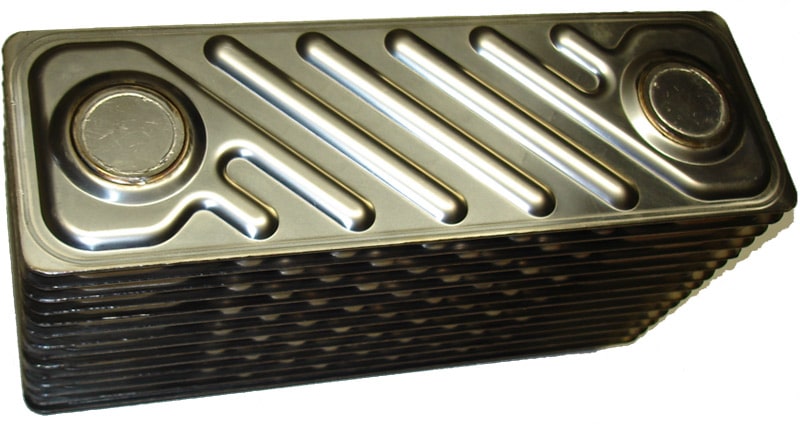
Solution: Design improvement
FluidForming’s Finite Element Analysis (FEA) and simulation software feature allowed our team to evaluate the part design prior to tool build. Using FEA data, our engineers took the client’s old design and manufactured the part with minimal springback and improved accuracy.
With a 99.996% first pass yield success rate, FluidForming offered the quality, accuracy, and repeatability our client needed. Because only one surface of the heat exchanger was subjected to the flexible and self-adjusting tool surface (recycled water), the resulting part was free from scratches, dents, or burrs. Furthermore, because of the negligible distance between the tool and metal surface, the resulting part was highly accurate. FluidForming’s high forming pressures also helped ensure that the completed heat exchanger experienced virtually no warping or springback. This, in turn, further minimized post-forming fixturing and clamping.
Unlike die stamping, which required quarterly tool maintenance and cost tens of thousands of dollars, tool maintenance expenses are minimal.
In fact, our solution proved to be so elegant and efficient that the client was able to convert their cumbersome and costly additive welding to a highly efficient, clamp-free stacked laser welding process.
Results: Higher quality and lower costs
Because the overall costs of FluidForming proved to be dramatically less than die casting (thanks to our Six Sigma process, improved production times, automated laser welding, and minimal die costs), the client purchased a FormBalancer machine and enjoys improved performance and lower costs.
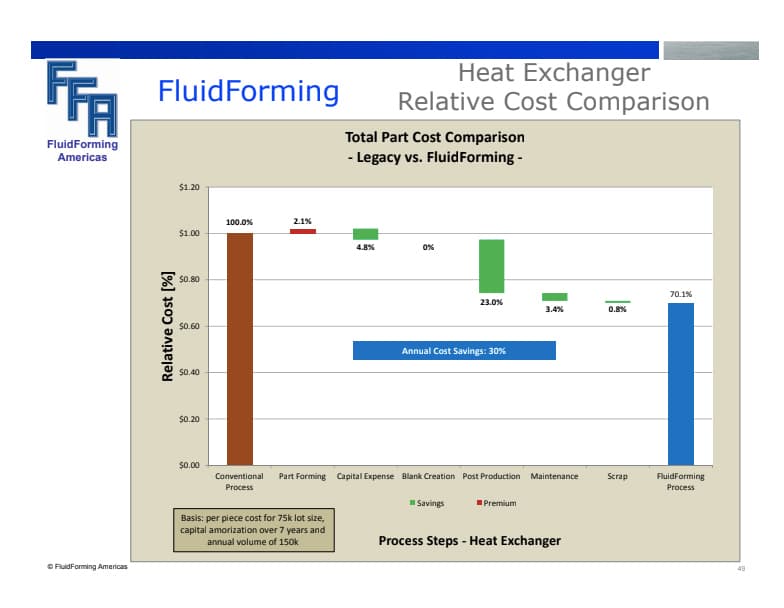
- 97% reduction in plate deflection and warping
- ~~4/1000” vs 1/10” (0.1 mm versus 2 – 3 mm)
- 99.996% first pass yield (Six Sigma process)
- .0043% failure rate
- ~~15 failures out of 350,000 units vs. a minimum of 17,500 failures out of 350,000 (5%) units
- 350,000 parts formed with no tool maintenance required
- Downtime eliminated
- Post-process fixturing and attendant costs eliminated
- FluidForming technology relies solely on recycled tap water and produces no emissions or harmful waste.
Summary: Higher quality conventional heat exchanger and improved overall profit margins
Have a metal forming problem that’s begging for a solution? To learn more about the FluidForming technology and process and to find out if our reinvention of hydroforming is right for your next project, contact FluidForming Americas at (800) 497-3545 or email us at info@ffamericas.com.