Overview: Forming a highly accurate and repeatable satellite dish
FluidForming Americas is known for hydroforming parts and components for extremely demanding industries and highly sensitive applications. Because the FluidForming process produces the highest levels of accuracy and repeatability, we have formed parts for the marine and aerospace industries as well as for use in military applications.
In this example, we’ll discuss a virtually flawless satellite dish that we formed for use in military and marine applications. What’s most remarkable about this piece of equipment is its absolute consistency and tight tolerances.
Problem: Poor performance, consistency, and repeatability
After experiencing unacceptable levels of metal spring-back and wall thickness variations in dishes formed by metal spinning, the client approached the FluidForming team to form an aluminum dish that had excellent microwave mirroring capabilities. Although they had a tremendous need for the surface to be sonically focused, their existing equipment had proven to be unreliable and was prone to missing critical satellite signals. Simply put, the client needed a satellite dish that resisted warping, was highly accurate, virtually flawless, and was incredibly repeatable.
Solution: Higher pressures = more accurate and highly repeatable parts
Unlike the legacy metal forming methods our client was accustomed to, FluidForming’s Six Sigma process experiences minimal warping, maintains unparalleled degrees of accuracy, and is highly repeatable. As a result, the new FluidFormed part dramatically improved incoming and outgoing signal quality.
Because just one surface of the satellite dish’s sheet metal is exposed to the flexible and self-adjusting tool surface (water) under variably controlled pressures, the aluminum is forced evenly into the tool and onto the tool surface. Consequently, the finished part has little to no distance between the tool and the metal surface, resulting in a highly accurate part and repeatable process.
With a 99.996% first pass yield success rate, the FluidForming technology and process guarantee quality, accuracy, and repeatability. With pressures up to 4x as high as those used by traditional hydroforming devices, the FluidFormed satellite dish experienced minimal warping or springback, which virtually eliminated post forming fixturing and clamping. If necessary, minimal springback can be compensated for by changing or deepening the tool surface.
Accuracy and repeatability data is verified through an optical scanning measurement process.
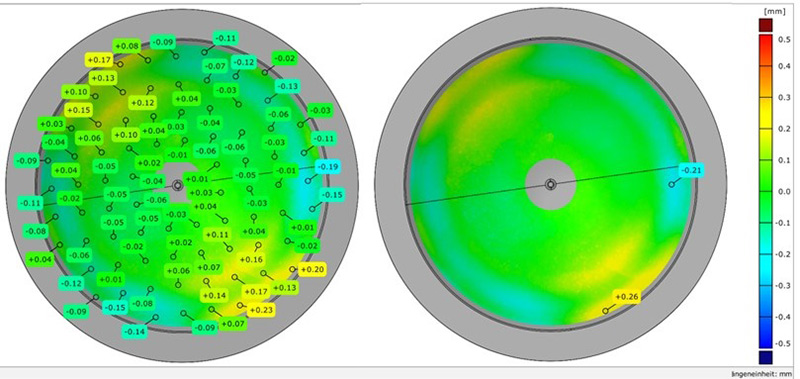
Results: unbeatable accuracy and higher quality
Parts and components formed using the FluidForming process and technology are extraordinarily precise, accurate, and durable.
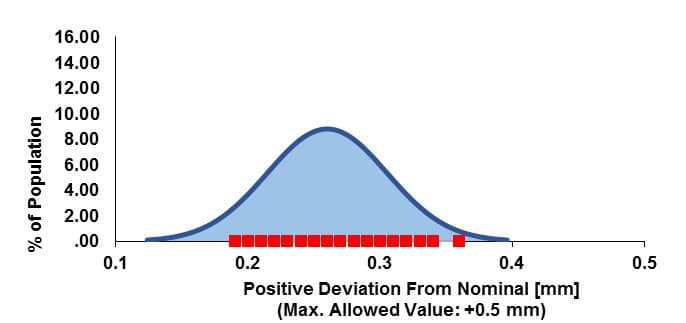
These results simply cannot be achieved using a legacy technology such as metal spinning, die stamping, “legacy” hydroforming, or die casting. Compared to these methods, FluidForming improves springback and warping by an order of magnitude and eliminates downstream operations such as fixturing and clamping, resulting in significant cost reductions.
SUMMARY: ENJOY BETTER PART QUALITY, ACCURACY AND LOWER OVERALL PRODUCTION COSTS WITH FLUIDFORMING
Summary: enjoy better part quality, accuracy, and lower overall production costs with FluidForming
To learn more about the FluidForming technology and process and to find out if our reinvention of hydroforming is right for your next project, contact FluidForming Americas at (800) 497-3545 or email us at info@ffamericas.com.