It may be the default metal forming method for many manufacturers, but the disadvantages of die stamping are worth considering. As manufacturers search for ways to bring new products to market as quickly as possible, it's easy to lose sight of the importance of quality, accuracy, and repeatability. In this article, we'll touch on a few of the most significant disadvantages of die stamping.
Disadvantages of die stamping
- Poor accuracy and repeatability.
- High tooling costs.
- Cannot accommodate rapid prototyping.
- Not suitable for small or mid-size production runs.
- Not an iterative process.
- High scrap rates.
- High post-fixturing costs.
#1: Poor accuracy and repeatability
Although progressive die stamping can yield accurate parts with complex shapes, material thinning is highly likely and part repeatability is poor. It also requires incredibly expensive permanent, progressive steel tooling.
Advantage of FluidForming
Thanks to incredibly high forming pressures, FluidForming is a Six Sigma metal forming process that uses a single die to produce components with minimal warping, unparalleled accuracy, and high repeatability rates.
#2: High tooling costs
Die stamping requires significant upfront, hard tool and die costs. Not to mention ongoing tool maintenance. Because both a punch and a die are required, tooling costs are significant with die stamping. If tooling changes are required or tools are damaged, additional costs are inevitable. Where possible, designs should be based on the use of existing dies for standard shapes and bends. The need to create a custom die for stamping will further increase initial tooling costs (Thomas).
Advantage of FluidForming
Because just one tool is needed from prototype through production, tooling costs are reduced by 50-90%. And, with 3D printed tooling, it's easy to make changes to your product design without incurring significant delays or prohibitive expenses. Furthermore, because water is the forming force, tool wear is also minimized.
#3: Cannot accommodate rapid prototyping
Outdated metal stamping methods — like die stamping — require costly and time-consuming tool development. Because of this, rapid prototyping is prohibitively expensive and ineffective with die stamping.
Advantage of FluidForming
All of FluidForming Americas' FormBalancer metal forming machines are compatible with 3D printed, metal sintered, steel, aluminum, and composite tools. In other words, it's possible to move from design to production in a matter of days.
#4: Not suitable for small or mid-sized production runs
For the same reasons die stamping isn't suitable for rapid prototyping, it just doesn't cut it for low-volume, or short-run productions, either. It's simply too expensive and tooling development and set-up take too much time.
Advantage of FluidForming
FluidForming is ideal for low- to medium- volume production runs. Our process can easily accommodate anywhere from 1 to a million parts per year. Because just one tool is needed, tooling costs are slashed. And as an added benefit, FluidForming uses the same tool from prototyping through production — which saves time and money.
#5: Not an iterative process
Product developers and product innovators are hampered by the inherent restraints that die stamping metal forming process imposes. Because tool development is so time-consuming and costly, product designers cannot innovate and iterate products as freely as they should.
Advantage of FluidForming
Not only do 3D printed tools save time, but they're dramatically less expensive. Plus, FluidForming Americas offers customers detailed pre-production Finite Element Analysis (FEA) reports which means we're iterating before production even begins.
#6: High Scrap Metal Rates
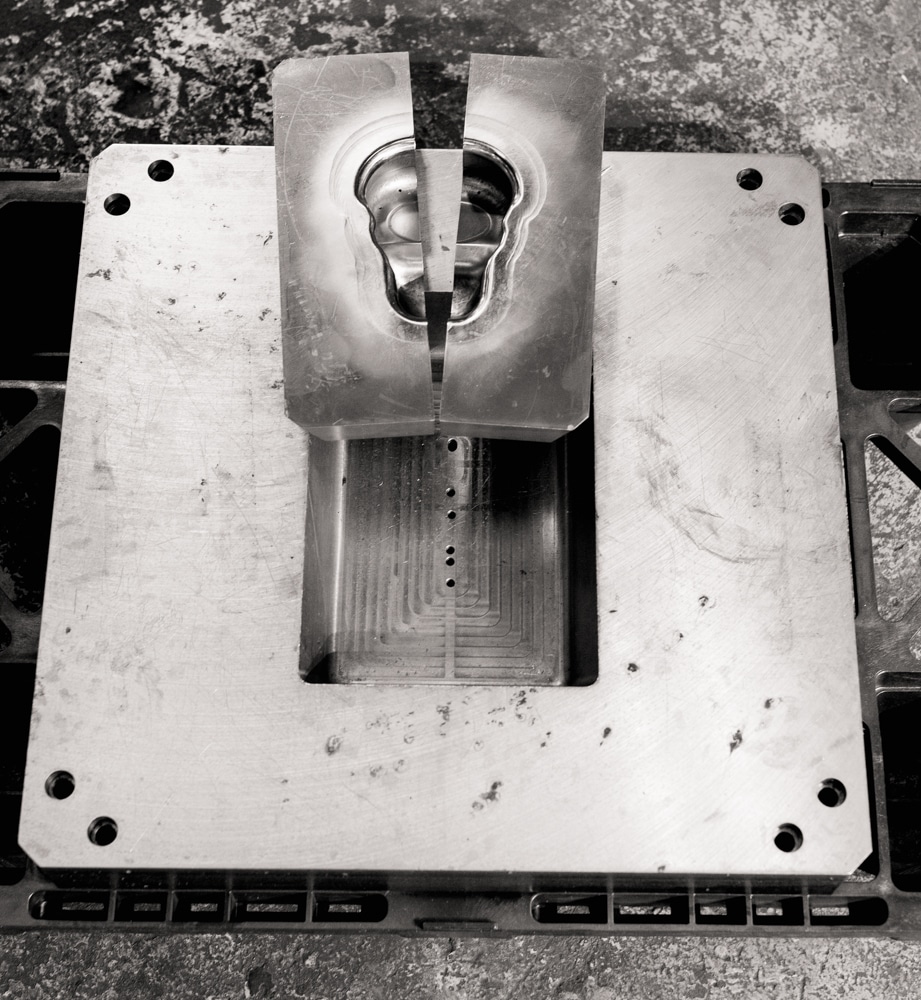
Although die stamping produces less scrap than machining, for example, scrap rates and non-conforming rates are high with die stamping.
Advantage of FluidForming
More and more manufacturers are focusing on reducing scrap because it's better for the environment, lowers production costs, and because it can result in faster turnaround times. FluidForming's 99.996% accuracy rate virtually eliminates non-conforming scrap and our nested tooling capabilities make the most of every inch of sheet metal.
#7: High Post-Fixturing Costs
Die stamping is a primitive stamping process that relies on brute force to deform metal into a predetermined shape. The process requires substantial post fixturing work like deburring, clamping, painting, and polishing. All of which adds time and cost to the process.
Advantage of FluidForming
Because the forming force — water — comes in contact with just one side of the material, post-fixturing costs are all but eliminated. The process is compatible with pre-finished, textured, painted, or polished materials.
Are you designing for tomorrow with yesterday’s metal forming technologies? Find out how our 21st Century technology can revolutionize the way your product design teams dream, innovate, and produce. Contact FluidForming Americas today at (800) 497-3545 or email us at info@ffamericas.com. Let’s start designing for tomorrow with today’s technologies.
FluidForming Americas, Inc. is a member of the Precision Metal Forming Association and is AS9100 Rev D, ISO 9001:2015 certified.