A Quick Guide to Sheet Metal Hydroforming
Table of Contents
- Introduction
- What is Sheet Metal Hydroforming
- How Sheet Metal Hydroforming Works
- Why FluidForming Americas?
- Key Benefits of Sheet Metal Hydroforming Over Traditional Methods
- Industries that Benefit from FluidForming Americas’ Hydroforming Process
Introduction
FluidForming sheet metal hydroforming is revolutionizing the way manufacturers approach metal forming.
As industries demand greater precision, efficiency, and sustainability, hydroforming has emerged as the preferred method for producing high-quality, complex metal parts. FluidForming Americas leads the industry in hydroforming innovation, offering a process that is not only precise but also environmentally friendly and well-suited for just-in-time manufacturing.
This guide explores the fundamentals of sheet metal hydroforming, its advantages over traditional methods, and how FluidForming Americas provides the best solution for industries requiring exceptional accuracy and sustainability.
What is Sheet Metal Hydroforming?
FluidForming sheet metal hydroforming is a specialized forming process that uses highly pressurized water to shape metal sheets into complex geometries. Unlike traditional stamping or deep drawing, fluidforming hydroforming uses just one tool, eliminates the need for hard tooling, and allows for more uniform material distribution, reducing defects and material waste.
How Sheet Metal Hydroforming Works
Traditionally, the process involves placing a metal blank over a die and applying a bladder full of hydraulic fluid to form the metal into the desired shape. FluidForming is a bladder-free process that enables greater precision and repeatability — without using hydraulic fluid or bladders. This method allows for:
- Greater design flexibility
- Increased material integrity
- Reduced tooling costs
- Improved dimensional accuracy
Why FluidForming Americas is the Best Choice For Precision Metal Forming
FluidForming Americas has redefined sheet metal hydroforming by developing an advanced process that outperforms traditional hydroforming and deep-draw stamping. Here’s why FluidForming stands out:
1. Unmatched Precision
FluidForming uses a proprietary, high-precision hydroforming process that applies uniform pressure to the metal blank, ensuring consistent wall thickness and eliminating stress points. This results in superior part accuracy, making it the ideal choice for industries that require tight tolerances, such as aerospace, medical, and automotive manufacturing.
2. Environmentally-Friendly Metal Forming
Traditional metal forming processes often involve excessive material waste and energy consumption. FluidForming’s process is more sustainable because:
- It eliminates the need for lubrication chemicals and wasteful machining processes
- It reduces scrap rates significantly
- It consumes less energy compared to conventional stamping
3. Just-in-Time Manufacturing Compatibility
In today’s fast-paced industrial landscape, manufacturers require flexibility and efficiency. FluidForming’s hydroforming technology supports just-in-time manufacturing by enabling:
- Rapid prototyping and short production runs
- Reduced tooling lead times
- Seamless transitions from prototyping to full-scale production
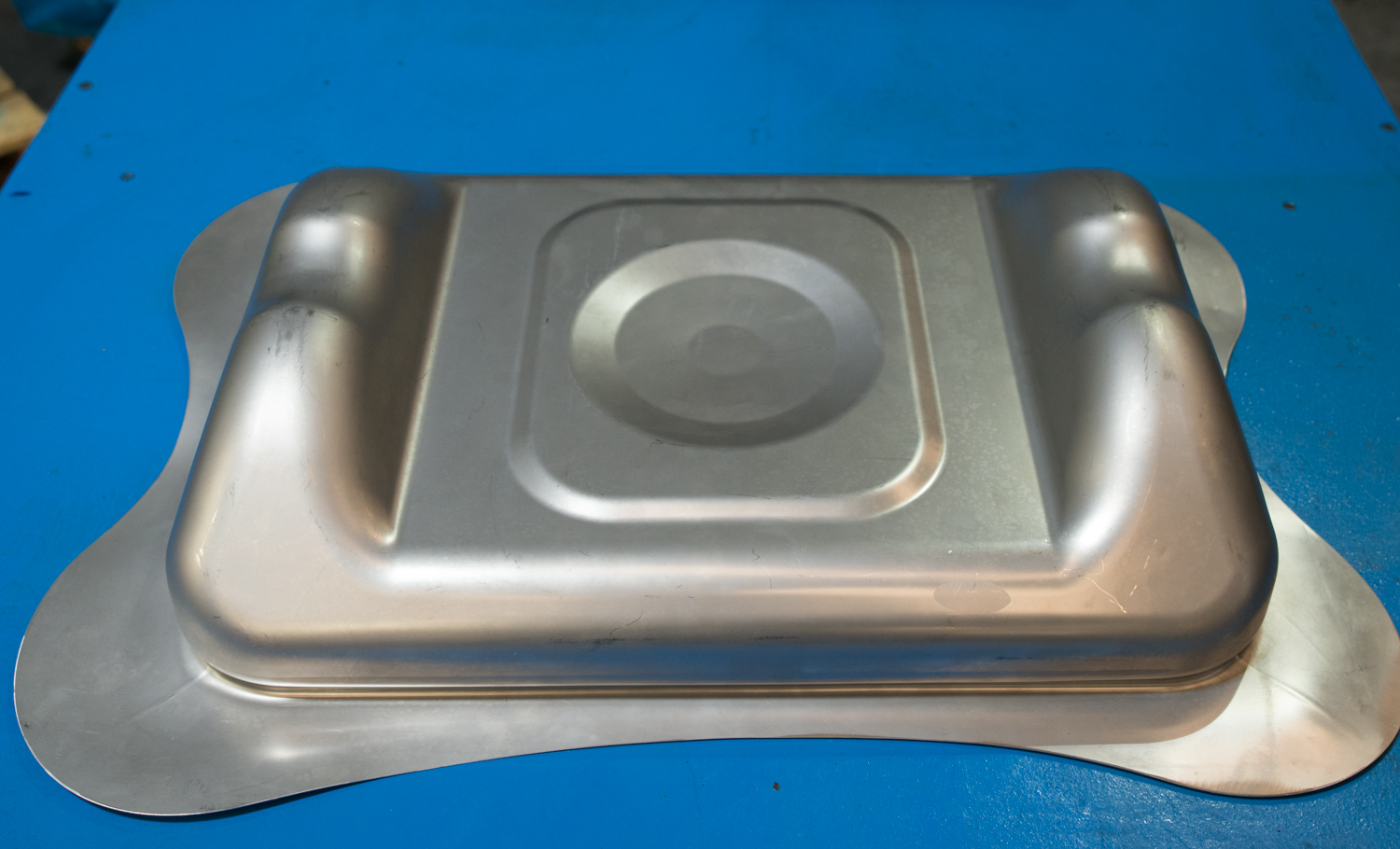
Key Benefits of Sheet Metal Hydroforming Over Traditional Methods
Hydroforming has distinct advantages over stamping, deep drawing, and other conventional metal forming techniques. These benefits include:
- Enhanced Design Flexibility: Hydroforming can create complex, lightweight structures that would be difficult or impossible with other methods.
- Lower Tooling Costs: Traditional stamping requires expensive dies that wear over time, whereas FluidForming hydroforming requires only a single die, reducing costs significantly.
- Improved Material Properties: Hydroformed parts maintain superior strength and integrity due to the even distribution of pressure during forming.
- Reduced Manufacturing Steps: Hydroforming often eliminates the need for secondary machining or welding, streamlining production and improving part consistency. Making it a great option for rapid prototyping.
Industries That Benefit from FluidForming’s Hydroforming Process
Many industries require the precision and efficiency of FluidForming’s hydroforming technology, including:
- Aerospace: Hydroforming allows for the production of lightweight, high-strength components that meet stringent quality standards.
- Automotive: Car manufacturers benefit from hydroformed structural components that improve vehicle safety and fuel efficiency.
- Medical Equipment: The precision of hydroforming ensures the production of high-quality medical device components.
- HVAC & Industrial Applications: Hydroformed metal parts enhance performance and longevity in heating, ventilation, and air conditioning systems.
Conclusion
Sheet metal hydroforming is the future of precision metal forming, and FluidForming Americas leads the way with an innovative, environmentally-friendly, and cost-effective approach. By offering unparalleled accuracy, reducing waste, and supporting just-in-time manufacturing, FluidForming’s hydroforming process is the optimal solution for industries requiring high-performance metal components.
Whether you're in aerospace, automotive, medical, or industrial manufacturing, FluidForming’s hydroforming technology provides the competitive edge you need. Contact FluidForming Americas today to learn how our advanced hydroforming process can revolutionize your production line.