Precision Metal Forming Manufacturing Solutions: How FluidForming Americas is Changing the Industry
In today’s competitive manufacturing landscape, finding reliable and efficient metal forming manufacturing solutions is crucial for businesses across all industries. From automotive and aerospace to medical and consumer electronics, manufacturers require precision, consistency, just-in-time delivery, sustainable solutions, and cost-effectiveness to remain competitive.
FluidForming Americas is at the forefront of innovation, offering cutting-edge metal forming manufacturing solutions that redefine traditional metal forming processes.
What is Metal Forming?
Metal forming is a broad term that refers to various manufacturing techniques used to shape metal into desired components without adding or removing material. These processes include stamping, hydroforming, deep drawing, and roll forming. While traditional methods have been used for decades, advancements in technology now allow for greater precision, efficiency, and sustainability.
The Challenges in Traditional Metal Forming
Traditional metal forming processes often come with several limitations, including:
- High tooling costs: Conventional stamping and deep drawing methods require expensive tooling and dies.
- Material limitations: Some metals are difficult to form using traditional techniques, leading to waste and inefficiencies.
- Long lead times: Complex parts often require extensive setup and production times.
- Inconsistent quality: Variations in pressure, tooling wear, and human error can lead to inconsistencies in the final product.
- Environmental impact: Many traditional methods generate significant waste and require hazardous chemicals.
How FluidForming Americas Provides Advanced Metal Forming Manufacturing Solutions
FluidForming Americas has revolutionized metal forming with its proprietary FluidForming technology, an advanced hydroforming process that overcomes traditional limitations. Here’s how:
1. Precision and Complexity
FluidForming technology uses high-pressure water to shape metal against a single die, ensuring unmatched precision. This process allows for the production of highly complex geometries with tighter tolerances, making it ideal for intricate components in industries such as medical devices and aerospace.
2. Reduced Tooling Costs
Unlike traditional stamping and deep drawing, FluidForming requires only a single die, significantly lowering tooling costs. This advantage makes low- and medium-volume production runs more cost-effective, allowing manufacturers to bring products to market faster without incurring excessive expenses.
3. Increased Material Compatibility
FluidForming can be used with a wide range of materials, including stainless steel, aluminum, titanium, and even advanced alloys. This flexibility enables manufacturers to select the best materials for their applications without being restricted by process limitations.
4. Shorter Lead Times
Because FluidForming eliminates the need for extensive tooling, production setup times are reduced dramatically. This benefit translates to faster turnaround times, allowing businesses to respond quickly to market demands and design modifications.
5. Enhanced Product Quality and Consistency
With uniform pressure distribution, FluidForming ensures consistent part quality with minimal defects. Unlike traditional methods that may cause thinning, tearing, or uneven surfaces, FluidForming produces stronger, more reliable components with better material utilization.
6. Sustainability and Waste Reduction
Environmental impact is a growing concern in manufacturing. FluidForming is a green alternative to traditional metal forming, as it reduces material waste, eliminates the need for harmful lubricants and chemicals, and lowers energy consumption. Manufacturers seeking eco-friendly solutions can benefit from FluidForming’s sustainable approach.
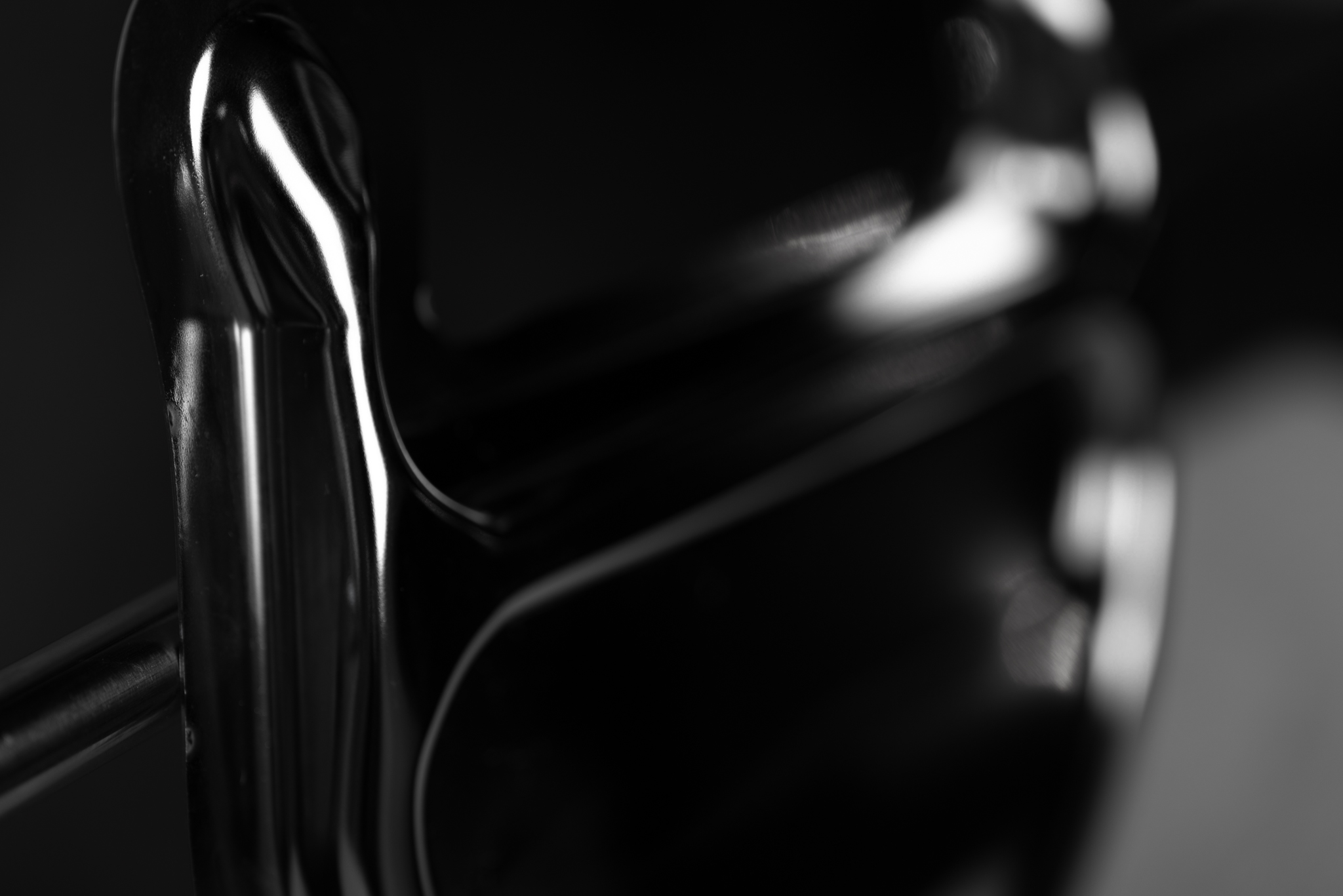
Applications of FluidForming Technology
FluidForming’s innovative approach to metal forming manufacturing solutions has been adopted by various industries, including:
- Aerospace: Lightweight, high-strength components for aircraft and spacecraft.
- Automotive: Precision-formed parts that enhance vehicle performance and safety.
- Medical Devices: High-quality metal components for medical implants, surgical instruments, and diagnostic equipment.
- HVAC & Energy: Durable and efficient parts for heat exchangers, turbines, and energy systems.
- Consumer Electronics: Sleek, intricate casings and enclosures for laptops, smartphones, and other devices.
Why Choose FluidForming Americas?
Manufacturers seeking reliable, high-quality metal forming manufacturing solutions can benefit from partnering with FluidForming Americas. Here’s why:
- Innovative technology that enhances precision, efficiency, and cost-effectiveness.
- Customization options to meet unique design requirements.
- Lower tooling costs compared to traditional metal forming methods.
- Eco-friendly processes that support sustainable manufacturing initiatives.
- Just-in-time manufacturing methodologies and capabilities
- Experienced team dedicated to delivering the best solutions for your industry.
As the manufacturing and metal forming industry evolves, businesses must adapt to new technologies that improve efficiency, reduce costs, and enhance product quality. FluidForming Americas is leading the way with its advanced metal forming manufacturing solutions, offering a game-changing alternative to traditional forming processes. By leveraging FluidForming technology, manufacturers can achieve superior results, streamline production, and stay ahead of the competition.
Level up your metal forming manufacturing solutions and elevate your production capabilities — contact us today to learn more about our precision forming solutions for the aerospace industry. Or, give us a call at 1-800-407-3545.
FluidForming Americas, Inc. is a member of the Precision Metal Forming Association and is AS9100 Rev D, ISO 9001:2015 certified. ITAR registered.