We’ve been hearing from our existing sheet metal hydroforming customers that they appreciate the level of service our team of metal forming experts and engineers have to offer. We’re leaders in the metal forming industry – and we do sheet metal hydroforming, but we do it differently! FluidForming Americas forms precision metal parts that work the first time. And the next time. And we do it on time. Every time.
There’s no great mystery to how we form metal parts that fit: it all comes down to physics. The fundamental physics of the FluidForming sheet metal hydroforming process differ significantly from conventional bladder-based hydroforming, metal spinning, or die stamping.
We Work Under (A LOT of) Pressure
With forming pressures of up to 60,000 psi (4,000 bar) FluidForming metal forming produces highly detailed parts with complex geometries. Thanks to the process’s high metal forming pressures – which are significantly higher than conventional hydroforming – FluidForming is capable of forming durable metal parts with a 99.996% first pass yield rate.
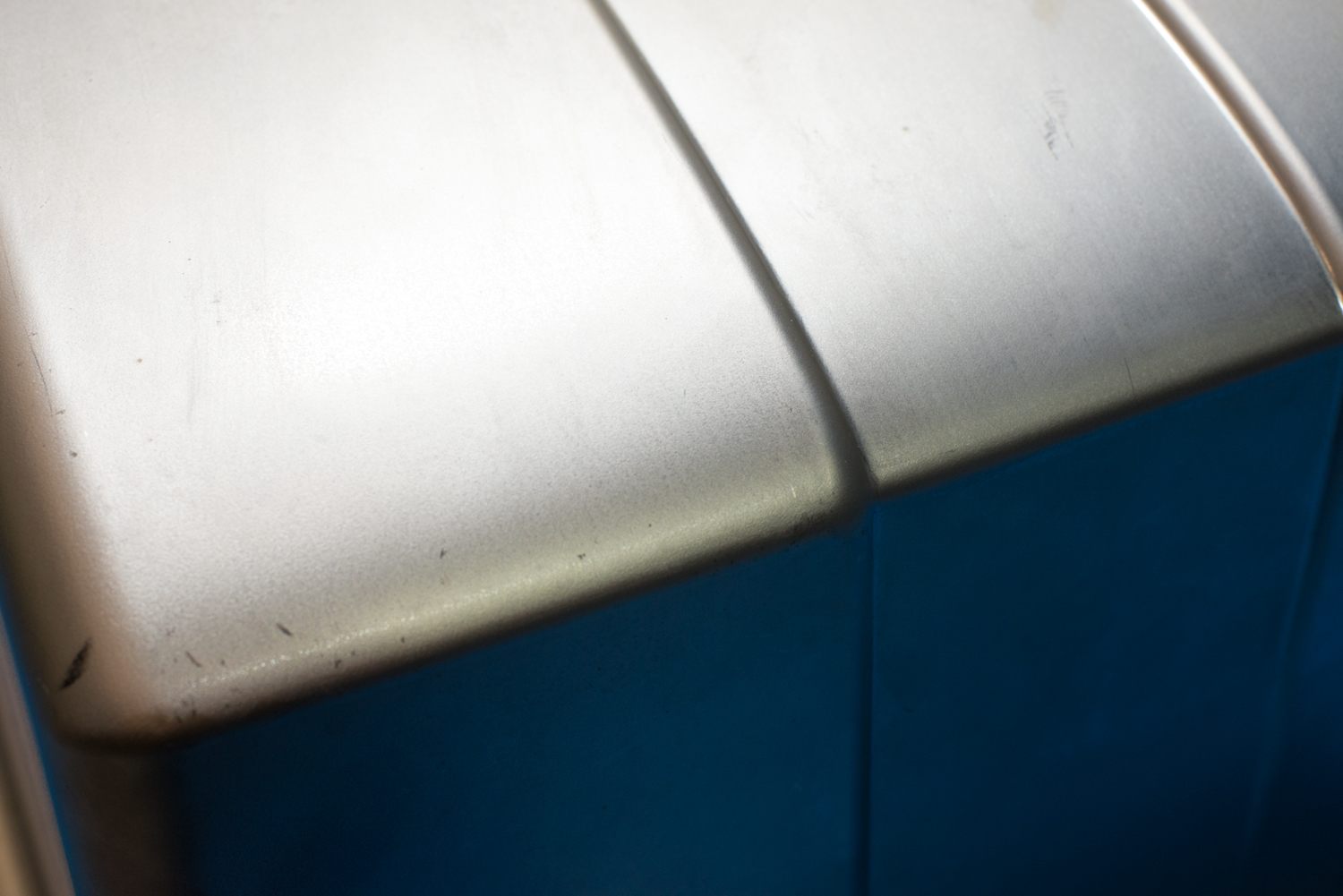
Our Bubbles Won’t Burst
Plus, FluidForming’s bladder-free technology simultaneously reduces maintenance costs and improves part precision and finish quality. Because the FluidForming process doesn’t require a bladder — unlike legacy hydroforming methods — the level of detail achieved by the process is unparalleled.
And, because only one side of the metal part comes in contact with the forming force – which is water – FluidForming produces beautiful unblemished parts.
Measure Twice, Form It Right
FluidForming Americas also offers finite element analysis (FEA) — which enables us to help customers like you make sure your product designs will work before a single piece is formed. FEA can also help manufacturers select the optimal material, find the perfect material thickness, and resolve any potential formability concerns before incurring forming costs.
Quality Advantages of FluidForming Metal Forming
- Six Sigma quality, accuracy, and repeatability.
- Eliminates bladder friction and tool marks.
- Accommodates the formation of complex shapes.
- Forms detailed impressions and microchannels.
- Accommodates undercuts.
- Minimizes springback and material thinning.
- Increases dimensional stability.
- Encourages creative and innovative design.
- Finite Element Analysis (FEA).
- Enables the use of pre-painted, polished, and patterned materials.
- Can form a single, functional part for prototyping.
- Excellent low- to mid-volume parts production.
Cost-Saving Benefits of FluidForming
- Reduces secondary operations or post-production fixturing.
- Uses a single die from prototyping through production.
- Reduces the use of consumables.
- Eliminates bladders and the risk of bladder ruptures.
- Lowers scrap costs.
- Minimal material waste.
- Nested tooling capabilities.
- Accommodates die inserts and product branding.
- Clean and quiet operation.
- Reduces overall energy costs.
- Shortens product development cycles.
- Accelerates time-to-market.
Expect great service. Contact FluidForming Americas today at (800) 497-3545 or email us at info@ffamericas.com.
FluidForming Americas, Inc. is a member of the Precision Metal Forming Association and is AS9100 Rev D, ISO 9001:2015 certified. ITAR Registered.