We’re in the news! FluidForming Americas is featured in FFJournal!
Paul Benny, CEO of FluidForming Americas, spoke with senior editor, Lynn Stanley, about the company’s highly accurate and repeatable precision metal forming process.
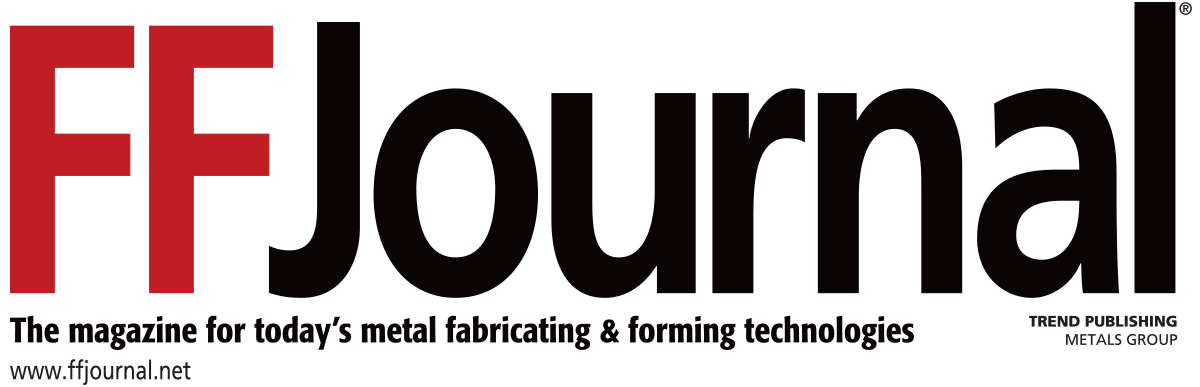
When it comes to fluid-formed parts, industrial users might have trouble believing what they see, but Paul Benny, CEO of FluidForming Americas, says, ‘There are no magic powders or mirrors. It is pure and simple physics that results in a highly repeatable, very accurate, cost-effective part.’
Founded in Hartsville, Tennessee, in 2014 as a German company’s North American subsidiary, FluidForming’s customers include Mercedes-Benz, BMW and Whirlpool Corp. Other end users run the gamut from aerospace, agricultural machinery and alternative energy to automotive and medical equipment.
Like hydroforming, fluidforming is a way of deforming ductile and malleable metal sheets and tubes into lightweight, durable parts. But that’s where the similarities end. Instead of hydraulic oil,
FluidForming’s FormBalancer uses tap water that has the capacity to shape metal at pressures of up to 4,000 bar/60,000 psi. The bladder-less, friction-less forming method is able to limit springback and material thinning, eliminates the need for consumables and can accommodate pre-painted, pre-polished and pre-patterned materials without degradation to a part’s surface.
Fluidforming is the reinvention of hydroforming, Benny says. ‘Legacy technologies have limitations and die stamping is not a controlled process. If you need an accurate, repeatable part that is pristine,’ he says, ‘physics renders these conventional methods incapable of that. Our physics is different. We aren’t limited.’
FluidForming Americas uses simulation and finite element analysis (FEA) to optimize part design and help customers determine material selection, thickness, formability and other variables. “This approach gives the customer a high degree of certainty about what the part will look like and minimizes their investment risk,” Benny says.
A single die (male or female) is then built and used for both prototyping and production. A nested tooling system means smaller dies with a range of properties can be used.
Fluidforming is a bladder-free process that uses water as the force to form.
Minimizing risk
A recent aerospace contract called for material thinning to be held at 17%. ‘We asked them how they had been doing the job up to this point and they told us they had never been able to control material thinning at 17%,” he says. ‘Our analysis confirmed a material thinning control rate of 12%. They didn’t believe us. We ran some prototypes and it turns out we were wrong: Material thinning was controlled at 11%, far exceeding the goal of the specification.’
— Excerpted From FFJournal’s March 2020 issue.
Read the full article!
Find out how FluidForming Americas is changing the metal forming industry. Contact FluidForming Americas today at (800) 497-3545 or email us at info@ffamericas.com.
FluidForming Americas, Inc. is a member of the Precision Metal Forming Association and is AS9100 Rev D, ISO 9001:2015 certified.
Save the Dates:
IMTS2020 | September 14-19, 2020 | Booth 236333 | North Building, Level 3
FABTECH 2020 | November 18-20 | Booth D46352 | Hall D