Find out how FluidForming Americas helps clients optimize parts prior to part formation.
Our committment to quality means helping our customers develop the best parts possible. Using finite element analysis, we are able to help refine parts during the development process. The helps our customers save time, money, and materials.
Be sure to read "Simulation Optimizes Precisio-Driven FluidFoming Metal Forming Process" at formingworld.com.
Here's a excerpt:
Forming the “Impossible”
In collaboration with J&N Metal Product, headquartered in Brazil, Indiana, the FluidForming engineering team used AutoForm to optimize part design for an aerospace manufacturer.
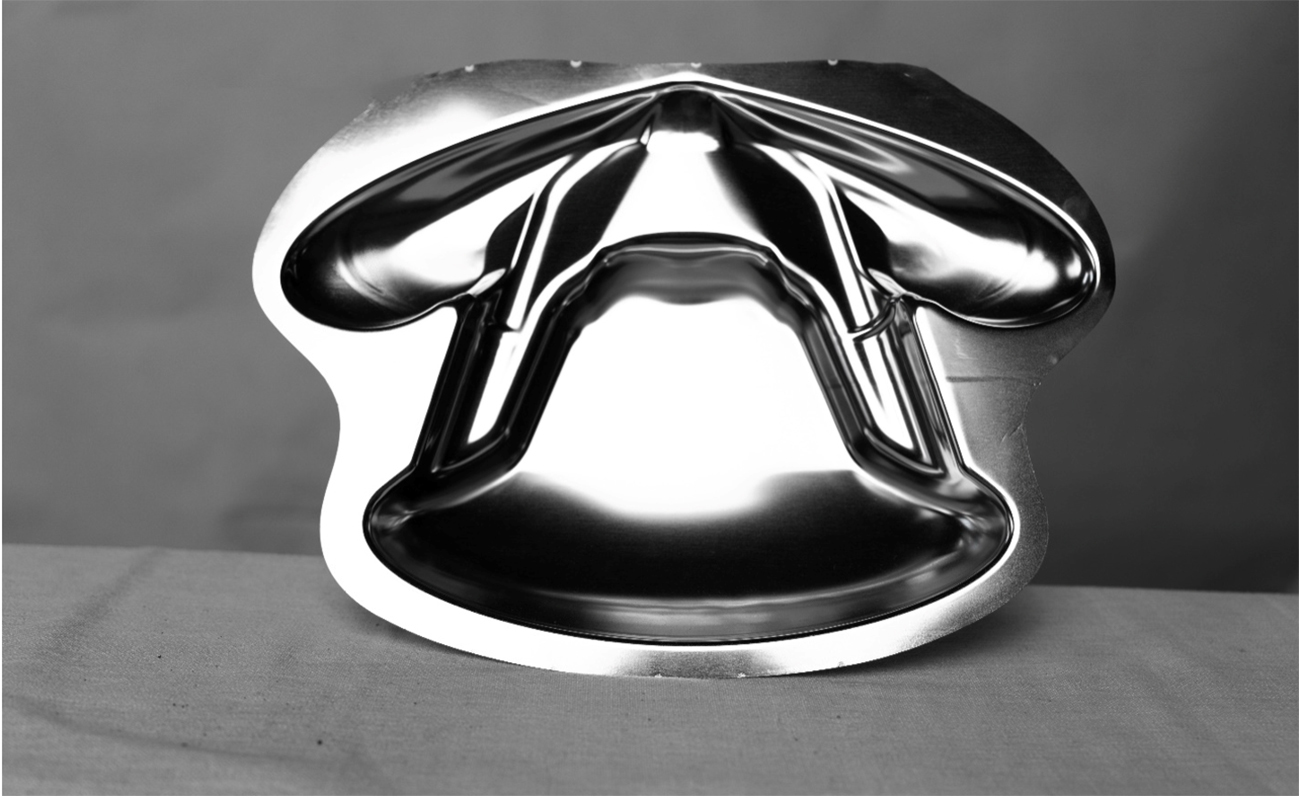
The image above is a prototype of a part produced for a well-known aerospace manufacturer. Formed from Inconel 718, the part measures 18” x 13.5” x 2.15” (L x W x D).
“The ‘Butterfly’ part was nearing un-manufacturable until we found Fluid Forming Americas. Working with them on the material thickness and orientation resulted in a usable part on a very complex assembly,” said J&N project engineering lead, Austin Eckstein.
The simulation allowed the engineering team at FluidForming Americas to conduct an initial review of the part in terms of formability and material thickness. From there, the team was able to provide feedback to the customer regarding the process’s forming feasibility. It also enabled the team to recommend possible design changes that improved formability.
In this instance, the team discovered that the initial approach with a single forming step would lead to material ripping due to the sharp corner in the tool to achieve the desired “butterfly” part shape. To ensure a successful and repeatable outcome, a nested two-tool approach with intermediate annealing was employed. This innovative solution resulted in less material thinning in the critical areas and no ripping.
The forming pressures needed to form out the full geometry of the part was 120 kPa (17,500 psi) and 90 kPa (13,000 psi), respectively, for the first and second forming steps. Formed from Inconel 718, the material thickness was held above 0.030″ with a starting thickness of 0.039″ which equates to a total thinning of about 23% and was well within the desired range for the customer."
Read the full article here!