Hydroforming starts with the Cincinnati Machine
Hydroforming is a metal forming process in which metal is shaped (or deformed) using fluid dynamics. Hydroforming yields lightweight, strong, and durable components. Like light reflectors, gear case covers, and heat exchangers.
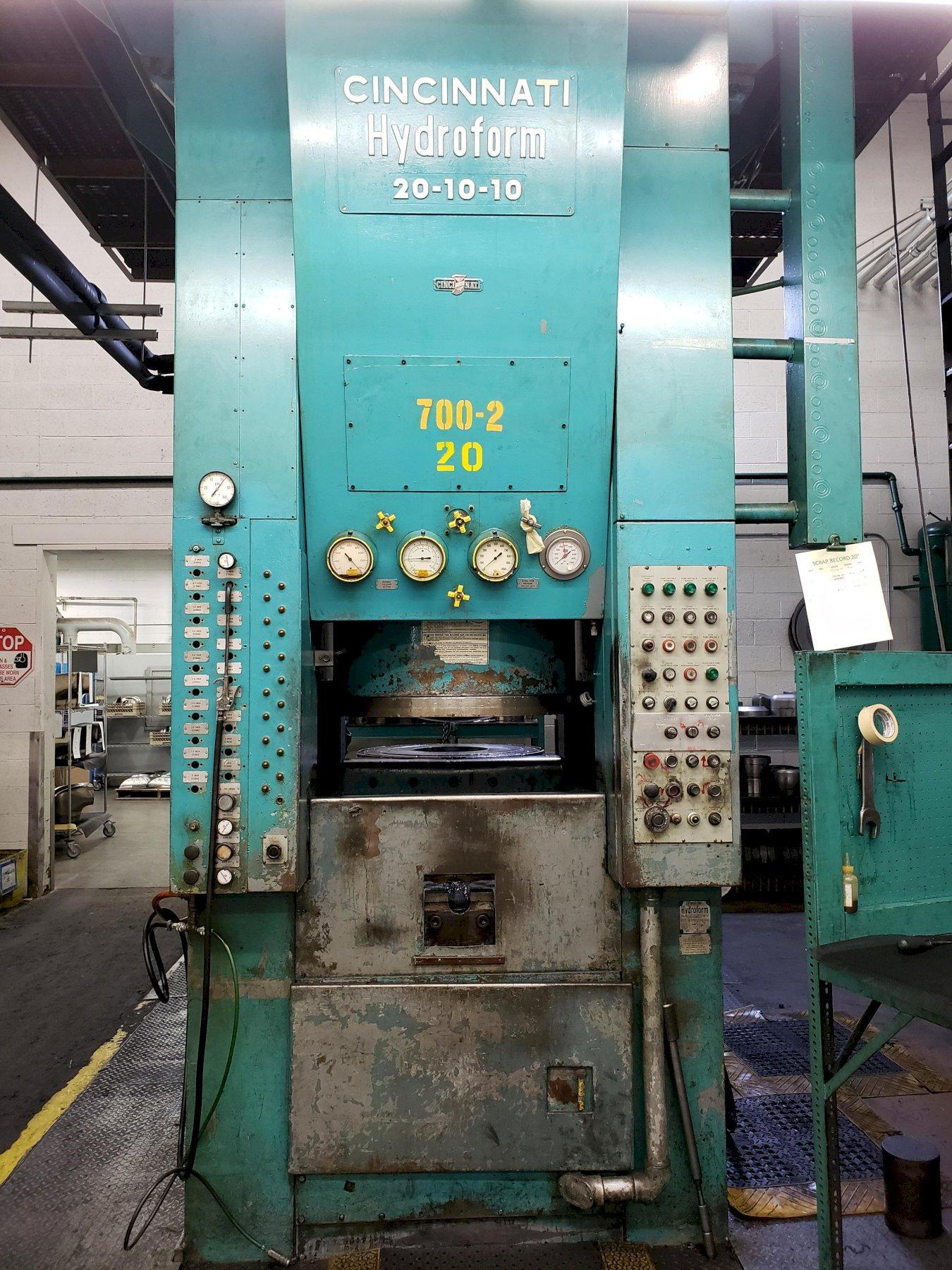
Although hydroforming has been around since the turn of the previous century, things really got rolling (or pressing) in Cincinnati in the 1950s. That’s when the famous Cincinnati Hydroforming process and the durable Cincinnati Hydroform press entered the picture.
The industry-changing Cincinnati Milling Company became known as Cincinnati Milacron in 1956, and the transformed business hit the market at just the right time! The jet age was upon us, and American automotive and aerospace manufacturers embraced new technologies and processes with open arms.
The then-new process allowed manufacturers to forego die casting, which produces heavy and less structurally sound components. And, unlike hydroforming, die casting was prone to metal stretch and required far more post-production finishing work than the components produced by the Cincinnati hydroforming process.
Although the machines were refined over the years, the technology would remain fundamentally unchanged until the turn of this century, when FluidForming was born.
Hydroforming of the Future is Known as FluidForming
Hydroforming is history. FluidForming is the sustainable metal forming process of the future.
The rugged Cincinnati machine workhorses have been a solid source for metal forming shops for many decades, but their days are increasingly limited. Machines are failing, replacement parts are hard to come by, and the components that today’s leading aerospace, automotive, and medical device manufacturers need are increasingly complex. And while hydroforming is more precise than die stamping, it isn’t more precise than FluidForming.
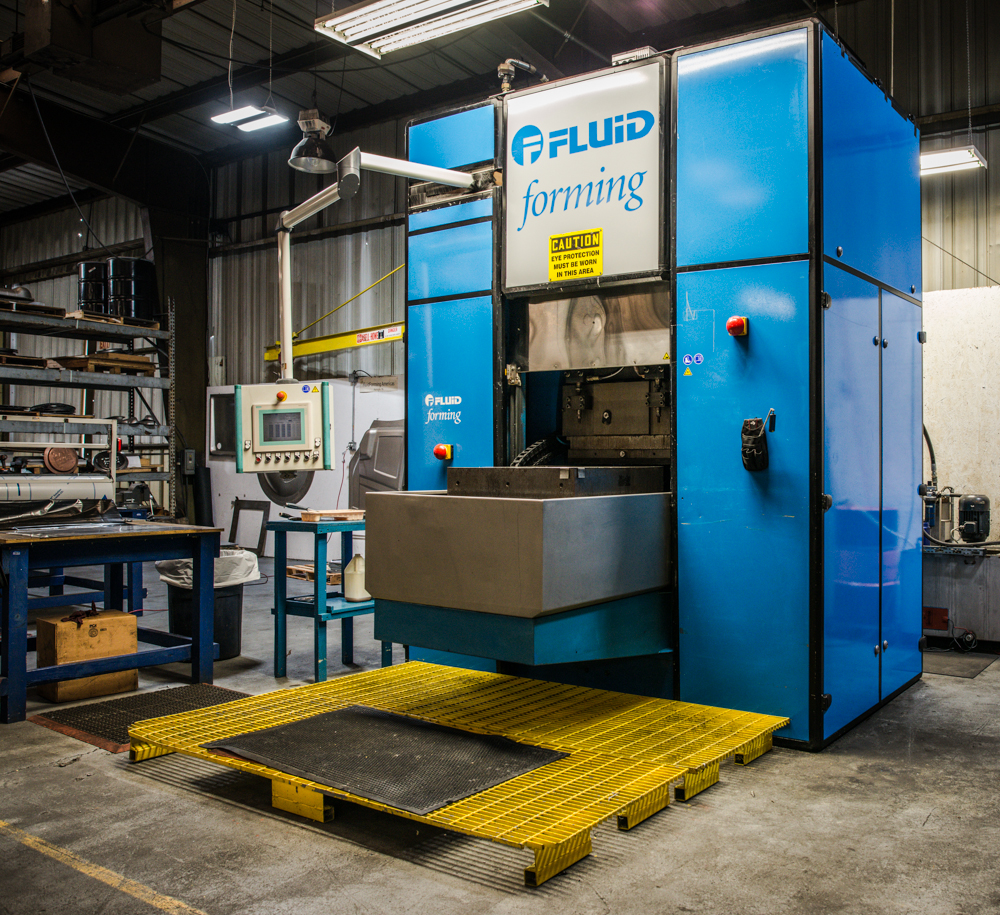
Like hydroforming, FluidForming uses fluid dynamics to shape metal and tubular parts, but the similarities end there. FluidForming is a bladder-free Six Sigma metal forming process. The force-contained FormBalancer machines use water as the forming force. FluidForming FormBalancer machines come in a variety of sizes and require minimal floor space.
It’s time to say goodbye to downtime, bladder ruptures, and non-conforming parts.
Moving Metal Forming Forward with the FormBalancer
The FluidForming FormBalancer is a force-contained press that achieves forming pressures of up to 60,000 psi. FormBalancers are available in a range of sizes and can be customized to your industry's -- or shop's -- needs.
FormBalancers are 4-in-1 presses capable of deep draw sheet metal forming, fluid cell sheet metal forming, optional bladder-based hydroforming, and tube forming.
The NEW FB40D model includes a dual sled for double the productivity. Contact us for more information.
It’s FluidForming Time
Get in on innovation. Embrace technology.
To reduce your carbon footprint and improve your precision metal forming and manufacturing processes, contact FluidForming Americas at (800) 497-3545 or email us at info@ffamericas.com.
Not quite ready to invest in a brand new metal forming press of your own? We can form precision components for you!
FluidForming Americas, Inc. is a member of the Precision Metal Forming Association and is AS9100 Rev D, ISO 9001:2015 certified.
VISIT US AT FABTECH 2022 in Atlanta, November 8-10. Georgia World Congress Center, Hall B Booth B5852