Fly Higher With Lighter, Stronger Parts
Regular readers of this blog already know that the FluidForming process shines brightest when tolerances get tight: the FluidForming FormBalancer 4-in-1 press delivers greater accuracy at a lower tooling cost than the legacy models it replaces.
For industries that place a premium on precision, like the aerospace and aviation sectors, FluidForming’s promise of rapid prototyping, consistent accuracy and durability, and compatibility with specialty metals is a perfect fit.
If you haven’t been following along, though, here’s a countdown of facts and figures that will introduce you to the FormBalancer and to FluidForming’s sustainable, high-accuracy manufacturing practices.
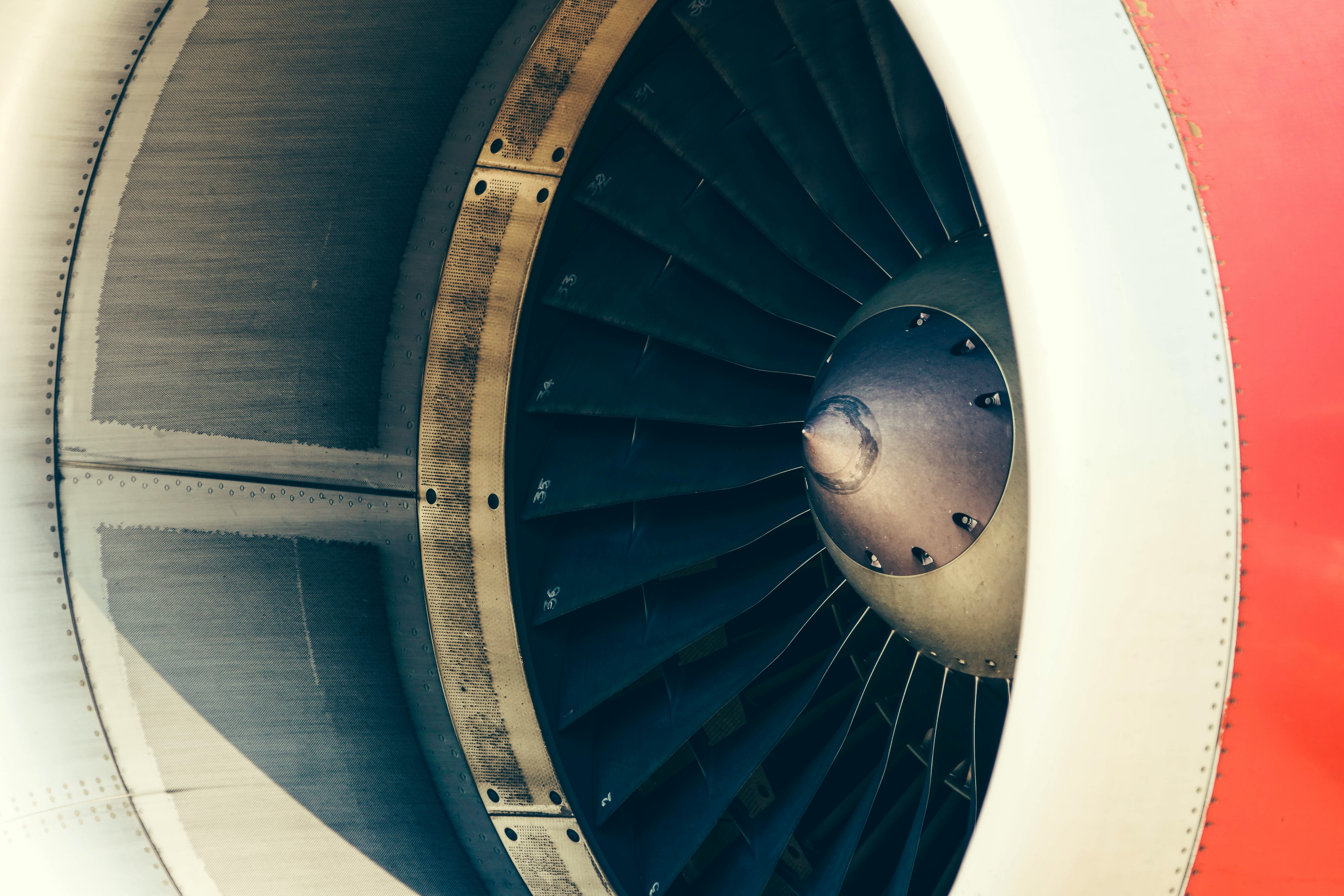
Increasing Demand for Precision Metal Fabrication & Aerospace Parts
Way back in 2018, we reported that the metal forming market was booming with a strong forecast for growth in the US aerospace industry. A lot has happened since then that we couldn’t predict, but we were right about FluidForming’s compatibility with the aerospace sector and about the growing demand for affordable, durable, highly accurate manufacturing for aircraft.
Pent-up post-pandemic demand, coupled with the rapid adoption of emergent technologies, means that we’ve seen even higher projected growth rates than we expected.
Specialized Aerospace and Aviation Metal Forming Production
As innovative aerospace manufacturers adopt new materials and technologies, the FluidForming FormBalancer keeps pace. The FormBalancer operates with up to four times the pressure of traditional hydroforming presses—up to 4,000 bar or 60,000 psi. This allows aerospace engineers to work easily with modern high-tech materials like titanium, stainless steel, copper, aluminum, nickel alloy, and more.
The FormBalancer makes production of highly specialized equipment equipment and components rapid, accurate, and sustainable—for instance, the FluidForming process makes emergent fuel cell production more affordable and more easily adoptable.
Cleared for Takeoff
FluidForming Americas is one of the leading metal forming companies that’s cleared for takeoff. Because FluidForming works seamlessly with CAD, 3D printing, and additive technologies, it dramatically reduces tooling and die costs, and enables a rapid prototyping cycle that moves from ideation to production in days rather than months. FluidForming backs up this rapid prototyping capability with detailed pre-production Finite Element Analysis to ensure that prototypes are optimized for real-world use conditions.
Small Tolerances, Large Format = Precision Aerospace Manufacturing
The accuracy, repeatability, and low environmental impact of the FluidForming process place it miles ahead of traditional sheet metal forming. And for aerospace and aviation applications, the range of lightweight, force-contained FormBalancer models ensures that even large format parts can be produced on FluidForming machines.
4-in-1 Metal Forming Flexibility
Far from a single-purpose sheet-metal press, the FormBalancer hydroforming press can take on a range of metalforming functions. One of the key benefits of owning a FormBalancer is its flexibility: it’s the only metal forming machine on the market that is able to deliver bladderless sheet metal forming, deep draw hydroforming, and fluid cell hydroforming. And for legacy bladder-based or hydraulic metal forming needs, the FormBalancer can be configured to use a bladder, too.
With the FormBalancer, FluidForming Americas takes a giant step forward in precision metalforming. To learn more about the FormBalancer’s capabilities and benefits, contact FluidForming Americas at (800) 497-3545 or email us at info@ffamericas.com.
FluidForming Americas, Inc. is a member of the Precision Metal Forming Association and is AS9100 Rev D, ISO 9001:2015 certified. ITAR registered.