FluidForming is an environmentally friendly sheet metal forming process that helps critical industries improve sustainability.
FluidForming Americas has worked with aerospace engineers, optimizing aircraft components and making them lighter and more durable. Our highly experienced team has collaborated with automotive manufacturers to manufacture lightweight, efficient intake manifolds. The sustainable metal forming process has enabled solar panel manufacturers to integrate microchannel heat exchangers into state-of-the-art solar arrays. FluidForming is also the go-to reinvented hydroforming process for leading appliance manufacturers when they want to make sure their products look great and perform well.
More importantly, FluidForming is capable of metal forming food-safe valves. Why is that so important, you ask? Well, because flawless valves are easier-to-clean and therefore perfect for the brewing industry.
So yes, FluidForming is more sustainable than die casting. We’ll go so far as to say it’s the greenest, most eco-friendly metal forming process available to manufacturers. Unlike die casting, which is a remarkably energy-intensive process. “Molten metal processing is inherently energy intensive and roughly 25% of the cost of die-cast products can be traced to some form of energy consumption [1]. The obvious major energy requirements are for melting and holding molten alloy in preparation for casting” (U.S. Department of Energy, Office of Scientific and Technical Information).
FluidForming hydroforming produces components with unbeatable part accuracy and repeatability. Because the FluidForming sheet metal forming process minimizes stretching and tearing, thinner metals and lighter metal alloys can be utilized.
Be sure to check out our exhaust manifold case study.
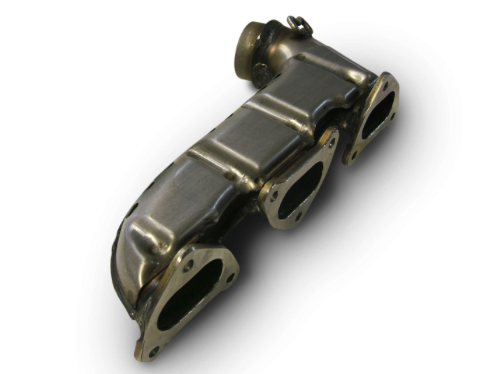
The FluidForming metal forming machine, the FormBalancer, relies on recycled water as the forming force. Which is also pretty darn green! As a reinvention of hydroforming, our technology enables innovation — and cost savings.
Sustainability experts around the country are embracing sustainable design and green manufacturing as a way to meet ambitious environmental goals and reduce harmful carbon emissions.
Take efficiency and a commitment to the environment to a new level with FluidForming
High energy costs, climate change, environmental impact, sustainability goals, and supply chain shortages are just a few reasons why manufacturers are turning to environmentally friendly, sustainable metal forming processes like FluidForming.
13 Ways FluidForming Can Shrink Your Carbon Footprint
FluidForming, as a sheet metal and tube forming process, has the 3 Rs of sustainability — reduce, reuse, and recycle — covered. And then some.
- FormBalancers are energy efficient.
- Recycled water is the forming force.
- Cold-forming metal forming process.
- Rejected waste heat can be recovered and recycled.
- Emission-free metal forming process.
- Reduce raw material waste.
- Eliminate non-conforming part waste.
- Blemish-free parts eliminate the need for downstream fixturing.
- Replace environmentally harmful foundry cast or plastic parts with metal.
To learn more about FluidForming, FluidForming Americas’ services, or to purchase a FormBalancer hydroforming metal press for your facility, contact FluidForming Americas at 1-800-497-3545 or email us at info@ffamericas.com.
Sign up to receive our newsletter.
FluidForming Americas, Inc. is a member of the Precision Metal Forming Association and is AS9100 Rev D, ISO 9001:2015 certified.