If You Own an Aging Cincinnati Machine, It Probably Is!
Purchasing a new hydroforming press is a big investment. We get it. For some companies, however, buying a new hydroforming machine is quickly becoming a top priority.
Why the urgency? Because the original presses manufactured by the Cincinnati corporation between 1930 and 1960 are rapidly hitting the end of their effective life. We’re freshly back from IMTS in Chicago where we heard tales — and saw the pictures — of Cincinnati hydroforming machines falling apart at the seams. So if you’re Googling phrases like “hydroforming machines for sale” or “replacement for Cincinnati hydroforming press,” we’re glad you found us.
Does Your Cincinnati Hydroforming Machine Need To Be Replaced?
If you own a hydroforming machine made by the Cincinnati company, the odds are pretty good that it's ready for retirement. After decades of wear and tear, many of these noble workhorses are nearing the end of the line.
Not only do aging Cincinnati hydroforming presses require an excessive amount of maintenance, but the parts needed to repair them are becoming increasingly hard to find. Downtime is becoming more and more common and lasting longer.
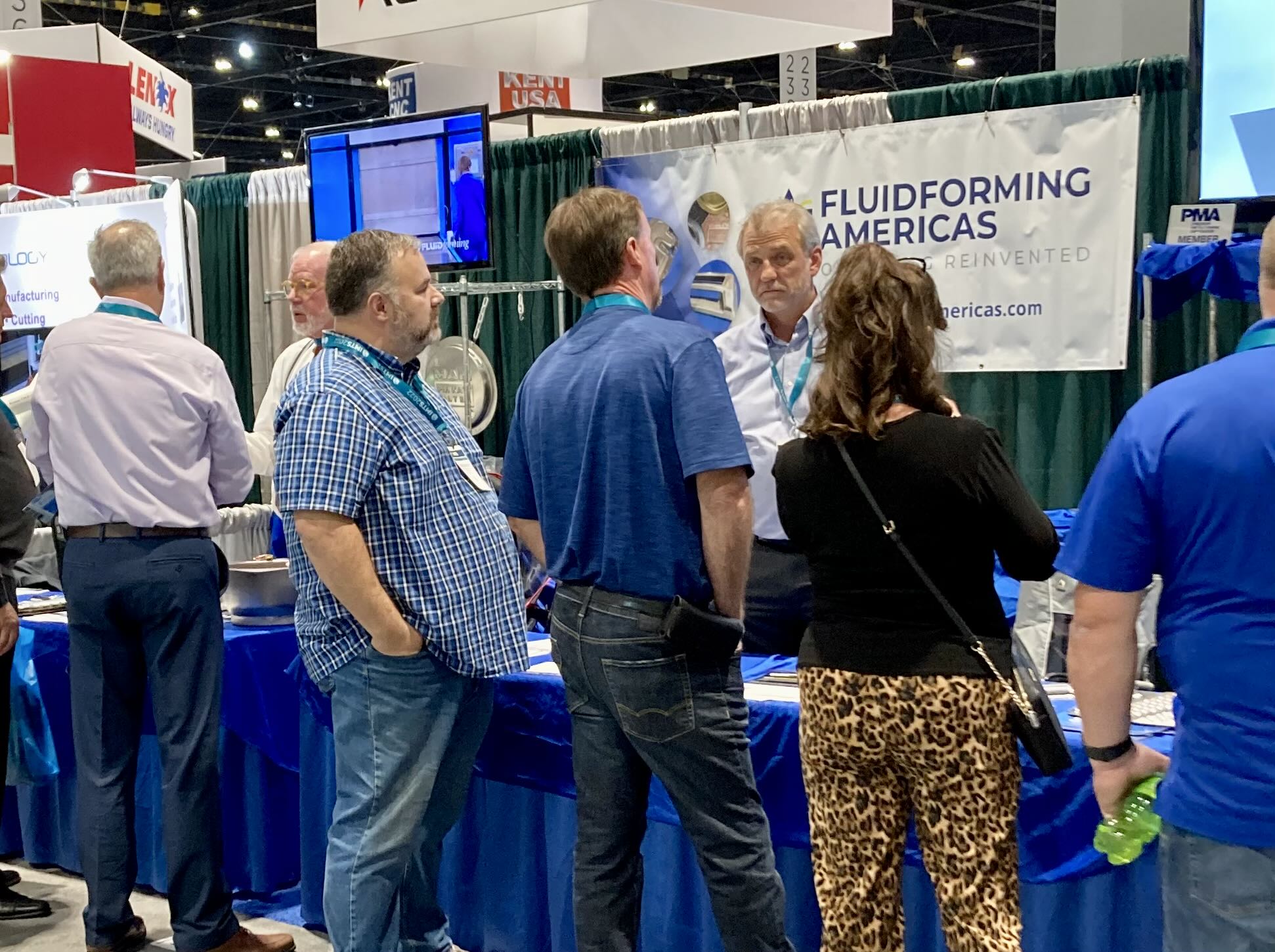
What to Consider When Buying a NEW Hydroforming Machine:
- Precision, accuracy & repeatability
- Tooling costs & requirements
- Deep drawing capabilities
- Finish & post-production fixturing
- Flexibility & dual-sled options
- Footprint & structural reinforcement
- Material compatibility
- Automation capabilities
- Sustainability and green manufacturing
- R&D Tax credits
- Exchange rates
- Overall value
Precision, Accuracy, & Repeatability: Why FormBalancers Make an Excellent Replacement for Cincinnati Presses
FormBalancers are bladder-free, deep draw presses that utilize the FluidForming technology. They eliminate costly, rupture-prone bladders and the need for environmentally harmful hydraulic fluid.
Force-contained FormBalancer FluidForming presses can achieve forming pressures of up to 60,000 psi. Our industry-leading forming pressure results in 99.996% accuracy and repeatability.
Minimal material waste combined with nested tooling capabilities and low tooling, operation, maintenance, and post-production costs can all help offset the cost of a new hydroforming press.
When precision, accuracy, and repeatability really matter, bladderless hydroforming comes out on top. The Six Sigma FluidForming process is ideal for the aerospace, medical, high-end home goods, and automotive industries. Other applications where precision metal forming may make a huge difference include three-dimensional designs, complex geometries, tight radii, and integrated lettering or branding.
Tooling: High Die Costs Add Up
Mechanical stamping presses and traditional hydroforming rely on progressive dies to achieve acceptable levels of precision. Progressive tooling is costly and time-consuming and damages the overall ROI of these machines. Nested tooling may be possible, but if progressive dies are involved, it becomes a costly and cumbersome process.
Typically the FluidForming process requires just a single die from prototyping through production. In other words, the prototyping tool is the manufacturing tool. The presses also accommodate 3D-printed tools and are compatible with nested tooling.
Deep Drawing: Form Complex Shapes, Achieve New Levels of Precision, & Make Better Products
If you’re looking to replace a Cincinnati hydrofoming machine, bladderless hydroforming methods are the wave of the future. They’re much better for non-standard deep drawing shapes like stepped, domed, or tapered parts. It also does a better job maintaining a constant material thickness, even over a tight die corner radius where other methods experience significant thinning. Logos, lettering, and integrated branding can be accommodated.
Finish: Consider Finish Quality and Post-Production Costs
For most manufacturers, post-production and fixturing costs are a completely different budget line from purchasing, but what if you could minimize (or eliminate) that line item altogether? If you’re manufacturing parts or components from pre-painted, textured materials, a bladderless FormBalancer machine can produce nearly flawless products that require minimal post-production fixturing — therefore lowering costs and improving time-to-market.
Flexibility: Get the Most out of Your New Metal Forming Machine
Mechanical stamping presses are fast, but they lack flexibility.
If process flexibility and flexibility in manufacturing capabilities are important business considerations -- think sheet metal forming and tube forming -- then purchasing a new, bladderless, force-contained press like the FormBalancer is the way to go. FluidForming FormBalancer metal forming presses offer users a high degree of control and variability throughout the entire metal forming process.
The FluidForming FormBalancer press is the only precision metal forming machine on the market capable of bladderless fluid cell sheet metal forming, deep draw hydroforming, and tube forming. In instances where bladder-based or hydraulic hydroforming would work best, the machines can also be configured to accommodate a bladder.
Plus, the brand-new dual sled FB40D FluidForming machine can double capacity and output!
Material compatibility: Lightweight is the New Heavyweight
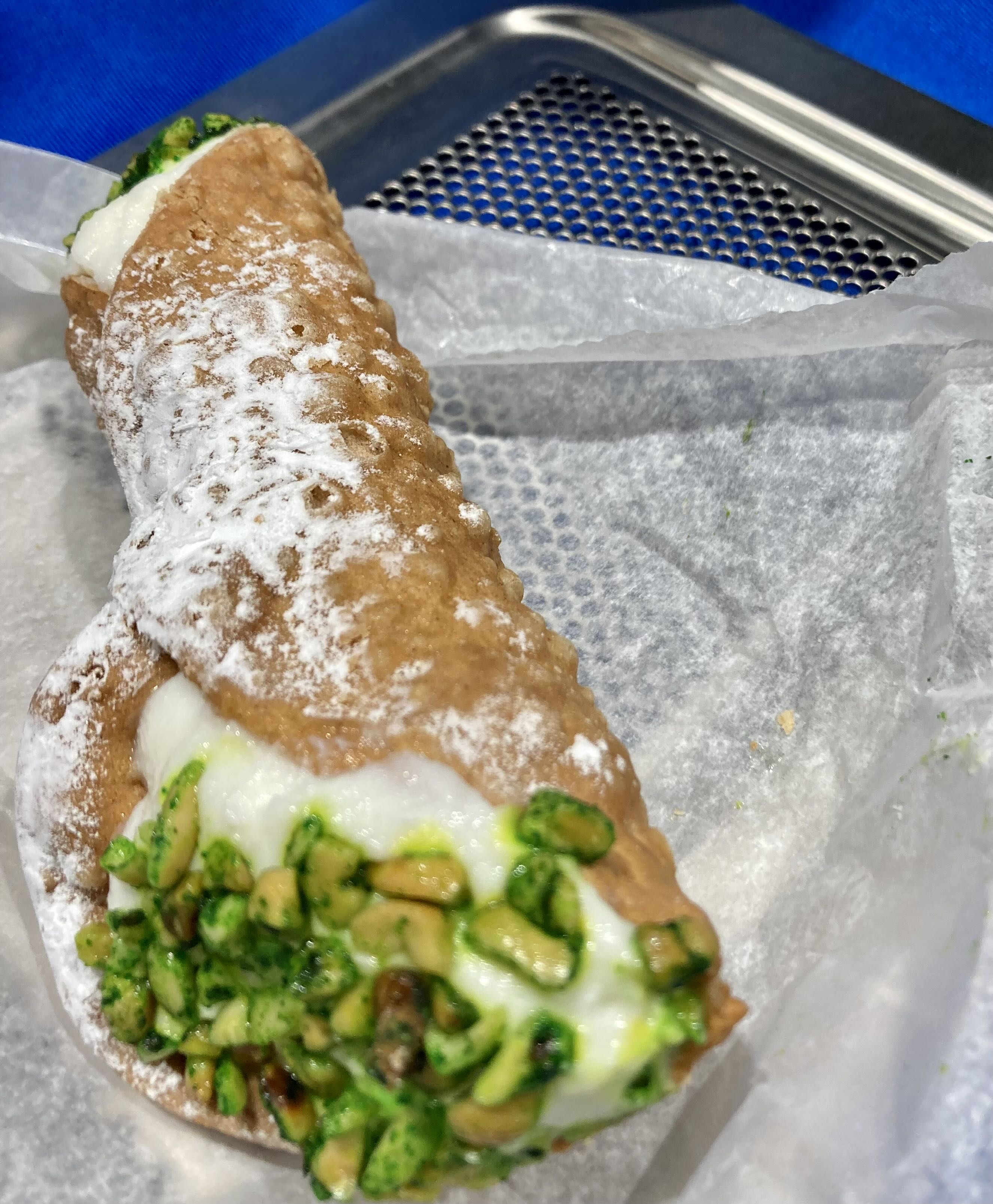
Between bites of D’Amato’s subs and cannolis, we managed to show off a number of FluidFormed parts produced by our in-house FormBalancer using the FluidForming process. From foil-like metals to tough and thick Inconel, the FormBalancer has proven itself to be a worthy upgrade from the classic Cincinnati hydroforming machine.
We also spoke with plenty of aerospace, energy, medical equipment, and automotive manufacturers, for example, all of whom are well aware of the value of strong and lightweight components — which improve part performance and can lower fuel consumption.
FormBalancer presses can accommodate a range of alloys and superalloys. Even aluminum alloys, which are notoriously prone to wrinkling and fracturing under stress, perform well with the FluidForming technology and FormBalancer presses.
Footprint and Structural Reinforcement: How Big is Too Big?
Small shop? No problem. Force-contained, bladderless presses like the FormBlanacer do not require additional footings or reinforcement. Compact, modular press design allows for flexible floor placement. Multiple machine and table sizes — which range from the FB25’s 800 mm x 800 mm to the FB100’s 1,500 mm x 2,000 mm — can accommodate a variety of jobs.
Automation: Improve Efficiency and Streamline Production
Sled robots and dual sled FormBalancer machines are available. Better automation capabilities also improve efficiency and help support sustainable manufacturing.
Sustainability: Making Manufacturing Greener & Lowering Operating Costs
As cold-forming processes, mechanical and hydraulic presses are infinitely greener than legacy die casting. However, energy consumption, material waste, hydraulic fluids, and other consumables render them less sustainable than bladderless metal presses.
For an even more sustainable option with low operating costs, consider a 480V FormBalancer press. The bladderless press relies on water as the forming force and draws just 90-200 kW of power, depending on machine size.
R&D Tax Credit and Favorable Exchange Rates
Yes, there’s a lot to consider when you’re shopping for a new hydroforming machine. Here’s a hot tip: Exchange rates are currently in the buyer’s favor. If we needed to replace our Cincinnati hydroforming press, we’d get the ball rolling today.
And let’s not overlook the potential value of the Research & Development Tax Credit! The R&D tax credit is available to companies developing new or improved business components. This includes new products or processes — like a new metal forming machine.
The R&D Tax Credit is a dollar-for-dollar tax savings that directly reduces your company’s tax liability. There is no limit to the amount of expenses and credit that you can claim each year. If the federal R&D credit can’t be used immediately, then the unused credit can be carried back for one year and forward for up to 20 years. State carryover rules vary. (Source: MossAdams).
To learn more about buying a metal forming machine for your facility, contact FluidForming Americas at (800) 497-3545 or email us at info@ffamericas.com.
FluidForming Americas, Inc. is a member of the Precision Metal Forming Association and is AS9100 Rev D, ISO 9001:2015 certified.