Metal forming industry & metal forming companies look to continued growth in 2019
Metal forming companies, rejoice! Despite new tariffs and labor shortfalls, the strong 2018 metal forming market will likely continue well into 2019. In fact, the global metal stamping market is expected to grow at a compound annual growth rate (CAGR) of 3.9% from 2018 to reach 289.2 billion (USD) by 2023 (Research and Markets). The United States gross domestic product is predicted to increase as well (The Fabricator).
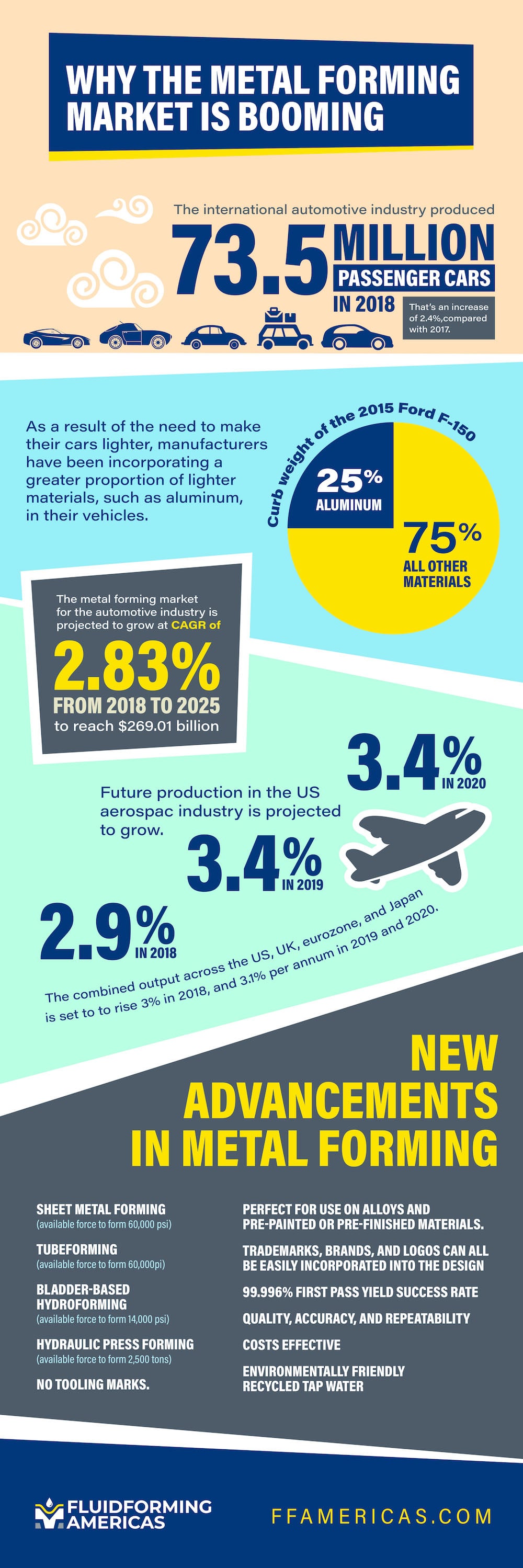
#1: Increasing urbanization and industrialization
Thanks to increasing urbanization and industrialization, metal forming companies such as FluidForming Americas are looking forward to a busy 2019.
The rising use of sheet metal throughout the manufacturing industries is helping to drive this growth. Affordable and reliable sheet metal forming is an important driver in industrialization. In recent years, the demand for sheet metal parts with different and complex shapes and properties has increased dramatically, due to the development of new technologies, products, and the evolution of modern industries (Science Direct).
#2: Growing Automotive Industry
According to recent data, the international automotive industry produced 73.5 million passenger cars in 2018, an increase of 2.4%, compared with the previous year. Although US car sales are predicted to wane in 2019, dozens of newly redesigned vehicles are hitting the market and overall worldwide sales forecasts are very encouraging.
Industry research also indicates that rising global vehicle production and growing commercial vehicle demand will further fuel the metal forming market. In fact, the metal forming market for the automotive industry is projected to grow at a CAGR of 2.83% from 2018 to 2025, to reach 269.01 billion (USD) by 2025 (ReportLinker).
#3: Changing Automotive Industry
“As a result of the need to make their cars lighter, manufacturers have been incorporating a greater proportion of lighter materials such as aluminum…in their vehicles. A case in point is Ford’s iconic F-150 pickup truck. Aluminum accounts for roughly 25% of the curb weight of the 2015 F-150” (Forbes).
Steel has long been king of the automotive industry, favored for its strength and safety; however, aluminum and other lightweight metals making deep inroads — all perfectly compatible with the FluidForming hydroforming technology. Which is good, because the hydroforming market is projected to show the fastest growth by forming technique segment (ReportLinker)!
The FluidForming technology is a modern reinvention of hydroforming. FluidForming was developed specifically to fill the market gap for a higher quality, cost-effective, accurate, fast, and intrinsically repeatable metal forming process. Mercedes-Benz, Porsche, and BMW have all turned to FluidForming for flawlessly formed metal components.
FluidForming is a bladder-free approach to traditional hydroforming that utilizes water at extremely high pressures (up to 400 mPA/60,000 psi). High forming pressures allow FluidForming to achieve a greater degree of detail, strength, and repeatability than any existing legacy method with minimal springback and warping. Because water comes into contact with just one side of the metal surface, it’s the perfect metal forming process for pre-finished metals and high-tech alloys that are commonly used in the industry.
#4: Increasing Demand from Aerospace and Aviation Industries
According to an article published by FlightGlobal in 2018, production in the US aerospace industry was projected to grow 2.9% in 2018, and 3.4% in 2019 and 2020. “The combined output across the US, UK, eurozone, and Japan is set to rise 3% in 2018, and 3.1% per annum in 2019 and 2020.”
These growth predictions are based on factors ranging from order backlogs, production plans by Airbus (also a FluidForming Americas client) and Boeing, low fuel costs, and “strong ongoing momentum in world trade.”
#5: New Advancements in Metal Forming
Advancement in metal forming such as FluidForming’s reinvention of hydroforming are revolutionizing how companies innovate and create. As technologies change and industries adapt to these changes, the need for affordable, durable, and highly accurate metal formed components is rising.
FluidForming, which works seamlessly with CAD, 3D printing, and additive technologies, lowers production costs by dramatically reducing tooling and die costs. The streamlined process also minimizes time-to-market, offering cutting-edge technologies a significant advantage in the marketplace. Unlike legacy metalworking methods, which can stretch production time over many months, FluidForming produces high-quality, production components in a matter of days.
The process’ high forming pressures virtually eliminate warping and springback, which minimizes post forming fixturing and clamping. Product designers, engineers, and executives appreciate the technology’s Advanced Element Analysis feature which allows for the evaluation of part design prior to tool build.
Learn more about the latest trends in metal forming and find out if the FluidForming technology is right for your next project. Contact FluidForming Americas today at (800) 497-3545 or email us at info@ffamericas.com.