The future of product design is here
Are your product design teams designing for tomorrow with yesterday's manufacturing technologies in mind?
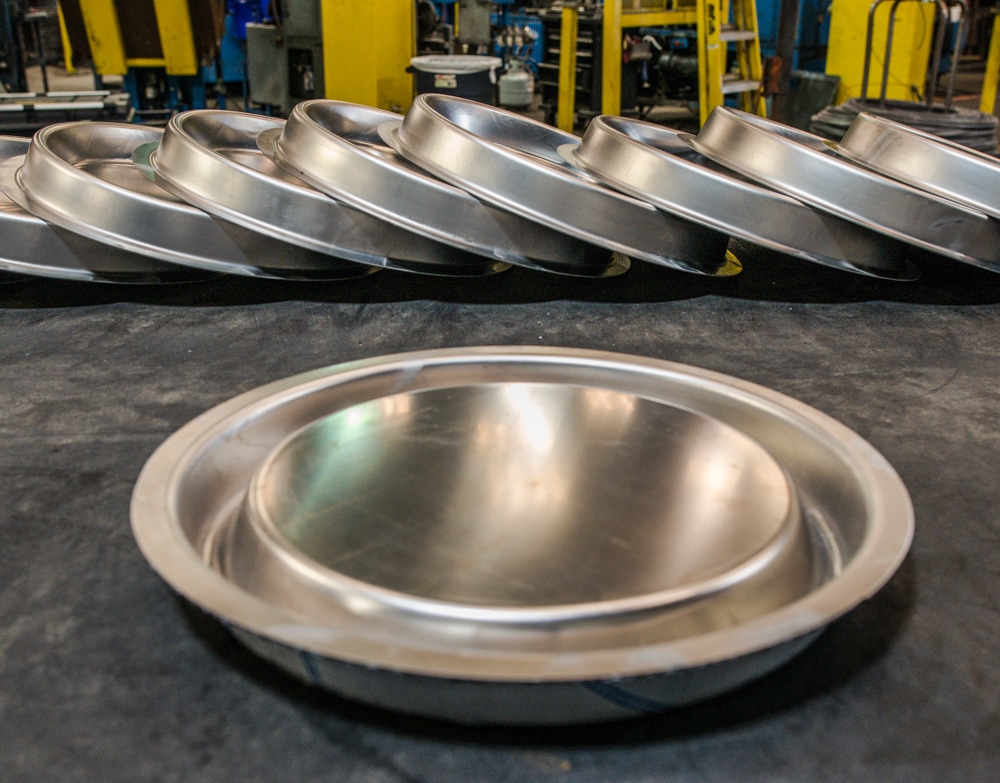
Innovation. Better living. Smart design. Lifehack. We hear the words nearly every day. Take a moment to scan your LinkedIn feed and you'll see countless videos of clever prototypes with of-the-moment hashtags like #productdesign #innovation #future #precisionmetalforming #industrialdesign. A quick look at Wired magazine yields fascinating articles about 3D metal jet printers and 3D-printed rockets.
Cool stuff, for sure. But a closer inspection reveals words like “slow” and “expensive” and “not practical.”
Which means most of those great ideas land in the scrap heap of time, right next to Frigidaire's “kitchen of tomorrow.”
It doesn't have to be that way.
Product design without compromise
Recently, we had the opportunity to meet with a very forward-thinking manufacturer who had this to say about product development and design:
We — and nearly everyone else in our industry — design new parts or make improvements to existing parts around the limitations of known metal forming technologies. In other words, our designs are only as good as the metal forming process we've always used. So we have always been very restricted in what we can do because of the limitations that die stamping, metal spinning, 3D printing, or conventional hydroforming impose on our designs.
Impressively, this company had gone so far as to create a custom manufacturing cell within its current production facilities. The new cell allowed them to gain efficiencies in operations, improve manufacturing flexibility, reduce labor, and improve time to market.
Which is great, but they missed out on some significant opportunities.
The force of FluidForming + the power of product design
Unfortunately, even with the new production cell, their gains were limited. Because their product design team had been working with 19th and 20th Century metal forming technologies in mind, they were limited by old-fashioned constraints.
Unlike other metal forming presses, FluidForming Americas' FormBalancer metal forming machines are bladder-free, force-contained structures capable of producing extremely high forming pressures of up to 4,000 bar/60,000 psi. Thanks to ultra-high forming pressures, the process results in a 99.996% first-pass-yield rate. Let's face it, better physics means better business.
The FluidForming difference
By redesigning their product with new-fashioned, 21st Century metal forming methods in mind � like FluidForming � they were able to:
- Improve part accuracy
- Improve part repeatability
- Improve product performance
- Improve product strength
- Improve aesthetics
- Improve customer appeal
- Improve automated assembly process
- Improve product life cycle
- Eliminate reworking of non-conforming parts
- Incorporate branding into product design
- Lower resistance
- Lower noise output
- Lower material costs
- Lower scrap rates
- Lower consumer operating costs
- Reduce drag coefficient
- Reduce labor costs
- Reduce material thickness
- Reduce overall weight
- Reduce material consumption
- Reduce energy consumption
- Improve overall quality
Find out how our 21st Century technology can revolutionize the way your product design teams dream, innovate, and produce. Contact FluidForming Americas today at (800) 497-3545 or email us at info@ffamericas.com. Let's start designing for tomorrow with today's technologies.
FluidForming Americas, Inc. is a member of the Precision Metal Forming Association and is AS9100 Rev D, ISO 9001:2015 certified.