Even your metal formed parts want to lose weight in 2022
Metal forming weight reduction is a resolution you can keep this year.
For some, ‘tis the season for fad diets and dry January. Here at FluidForming Americas, we always embrace the liquids but we’re all for shedding those extra pounds. Metal weight, that is. Our FormBalancer metal forming machine is primed and ready to help customers produce stronger, accurate, durable, and lighter parts in 2022.
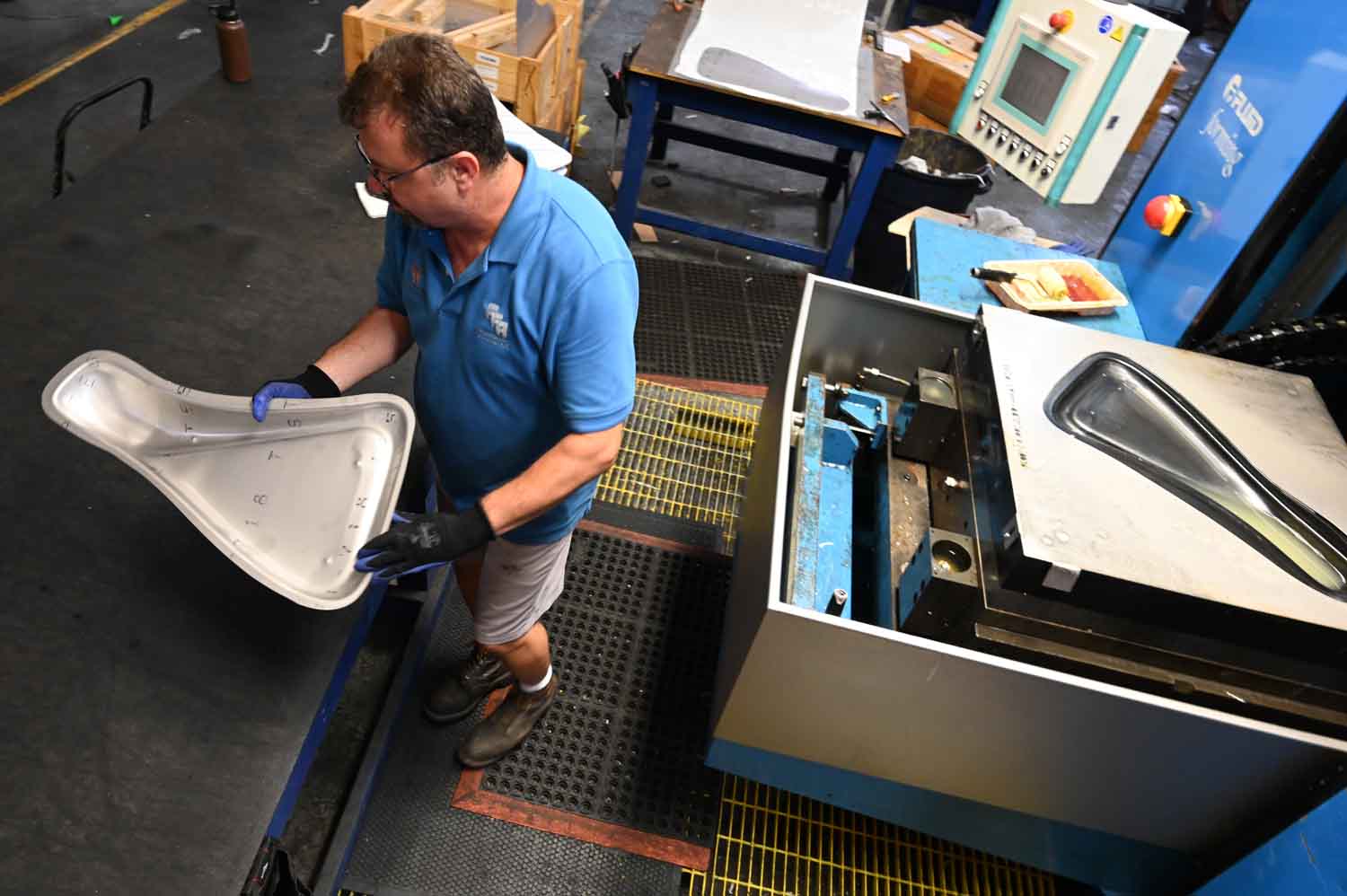
Trimming weight and trimming costs with FluidForming hydroforming
If you’re a product designer, entrepreneur, or inventor looking for ways to bring new and improved products to the market, you have a good reason to celebrate in 2022. New additions to the FormBalancer family offer metal forming shops even more options. Contact us to learn more about purchasing a new FormBalancer for your shop.
We’re also accepting orders for in-house production.
Reduce part weight by up to 50% with new metal forming technology
"Our experience shows that subject to specific needs, the weight reduction of a given part can be as much as 50%,” notes CEO, Paul Benny. “Obviously geometry, structural needs, dynamic load can be points of concern when it comes to metal forming weight reduction, but the usual culprit with heavy parts is over design or unfamiliarity with the newest metal forming methods — such as FluidForming.”
“Thanks to our finite element analysis capabilities, we’re able to work with our customers to help them optimize part design, before forming a single part. And in many cases, we can replace a “casting” with a much lighter-weight part. We’ve done this with pump housings, valves, and manifolds, for example. The weight reductions can be significant while simultaneously offering improved flow performance,” says Benny.
“Advanced materials are essential for boosting the fuel economy of modern automobiles while maintaining safety and performance. Because it takes less energy to accelerate a lighter object than a heavier one, lightweight materials offer great potential for increasing vehicle efficiency. A 10% reduction in vehicle weight can result in a 6%-8% fuel economy improvement. Replacing cast iron and traditional steel components with lightweight materials such as high-strength steel, magnesium (Mg) alloys, aluminum (Al) alloys, carbon fiber, and polymer composites can directly reduce the weight of a vehicle’s body and chassis by up to 50 percent and therefore reduce a vehicle’s fuel consumption” (Energy.gov).
In the metal forming world, lightweight is the new heavyweight
FluidForming is a great way to bring new products to market or improve product performance by reducing component weight. The FluidForming metal forming process was first introduced in Germany in 2000. Since then automotive giants, global appliance manufacturers, instrument makers, and solar panel manufacturers — to name just a few — have turned to FluidForming to improve the performance of their products by reducing weight.
Unlike conventional metal forming methods — sheet metal stamping, roll forming, die stamping, metal spinning, extrusion, and traditional hydroforming, we’re looking at you — FluidForming can achieve 99.996% first-pass yield rates. While keeping tooling and production costs low. Low-cost, low-weight rapid prototyping means the time between idea and production is dramatically reduced, which inspires creativity and ingenuity.
By applying uniform force to the sheet metal, the highly-pressurized recyclable tap water shapes the metal into the form of the male or female die. Oh! Did we mention that FluidForming requires just a single die, which further reduces costs? FluidForming’s extraordinarily high forming pressures of up to 60,000 psi ensures maximum deformation, allowing for highly detailed component production.
Benefits of FluidForming
The benefits of FluidForming are considerable. This new alternative to legacy metalworking reduces tooling costs by up to nearly 90%, promotes incredibly fast ideation to production turnarounds, and minimizes post-production operations.
FluidForming was developed to fill the market gap for higher quality, accurate, faster, intrinsically repeatable, and affordable metal forming. Flexible component designs offer endless possibilities for designers and engineers. If you’re looking for a highly accurate production process, our system offers enhanced design flexibility, reduces capital costs, minimizes time to market, and offers easy product branding. And yes, weight reduction is a sure thing.
To learn more about FluidForming and to find out how much weight your products can shed, contact FluidForming Americas today at (800) 497-3545 or email us at info@ffamericas.com