The best of FluidForming: 2021 edition
Time flies when you’re busy with the business of precision metal forming. With 2021 nearly in the rearview mirror, we decided to take a look at some of our biggest metal forming moments of 2021.
I went to the fortune teller, to have my fortune read.
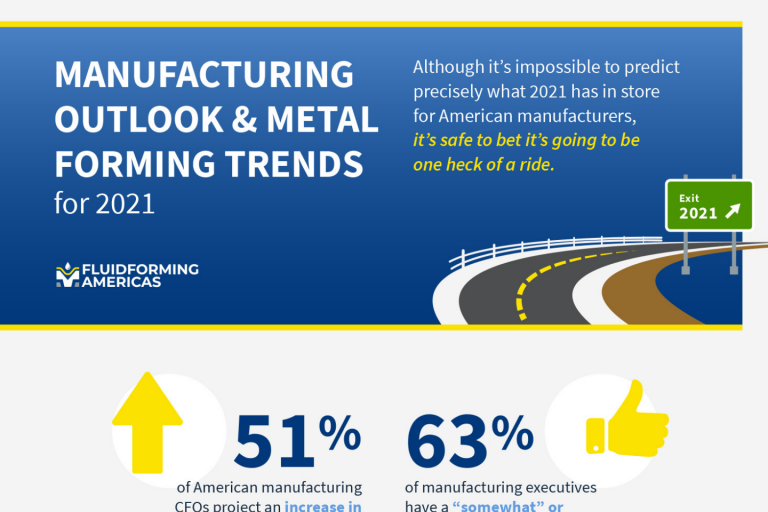
At the dawn of the year, we published an infographic highlighting the top metal forming trends for 2021. In it, we predicted that 2021 was going to be “one heck of a ride.”
Was it ever!
Our prognostications about 2021’s metal forming trends were just about as precise as our approach to hydroforming.
We noted that precision would become a higher priority and for many manufacturers, it certainly was. As supply chain woes mounted, finding an efficient, sustainable metal forming process with minimal material waste was critical.
We also predicted that sales of electric vehicles (EVs) would soar. Even with microchip shortages crippling the car industry, EV sales increased by 160% in the first half of 2021, representing 26% of new sales in the global automotive market (Power-Technology.com). We’ve been contacted by low-volume vehicle manufacturers who are interested in learning about how our new metal forming technology can improve their products and speed up their assembly lines.
We also said that “pent-up demand will fuel growth.” Need we say more?
FluidForming was featured in the fabricator.
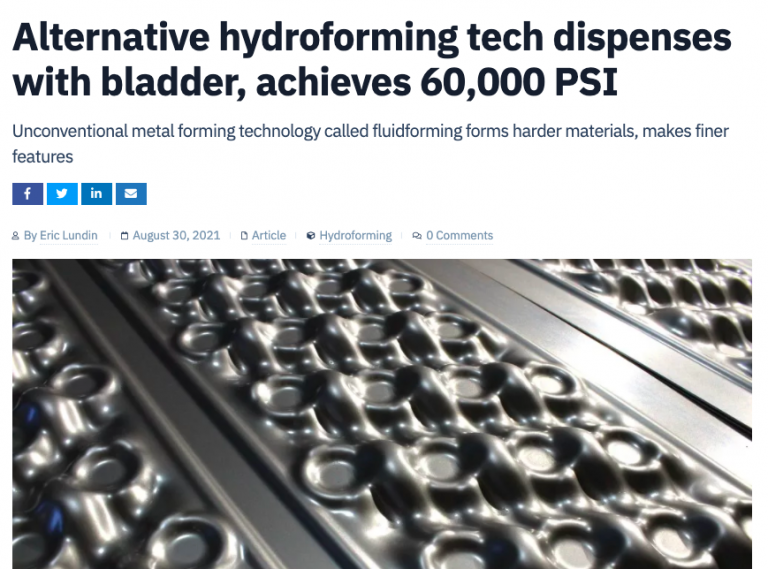
In case you missed it, now’s the perfect opportunity to read Eric Lundin’s great article about FluidForming and the FormBalancer’s capabilities in “The Fabricator.”
Our alternative hydroforming technology caught his eye and of course, Jurgen Pannock (Chief Technology Officer) and I had plenty to say. Here’s a quick excerpt:
“Because material flow is a part of the forming process, it doesn’t generate the forming marks that are often associated with hydroforming or stamping,” said Pannock.
“While the quality of the die matters, the bigger factor is that the forming process doesn’t sandwich the material between two mated dies and doesn’t have a bladder that interferes with the metal deformation,” he said. “This makes it possible to make undercuts, organic forms, deep-drawn parts, and other challenging parts that would either be impossible to form or prone to wrinkling when made with other processes or traditional hydroforming.”
Beyond forming difficult and intricate shapes, the process produces parts with very good surface characteristics.
“For kitchen applications like mixing bowls and baking pans, parts come out nearly ready to ship,” said Paul Benny, the company’s CEO. “Often the parts need a quick polish and that’s it.” As such, it’s compatible with prepared surfaces that often are damaged by forming processes, such as polished, patterned, and etched materials.
The same surface characteristics also play out well in forming a valve body.
“Traditionally, valve bodies are cast, and castings are porous,” Benny said. “Fluidforming enables the substitution of one-piece porous casting with a valve body made from two formed hemispheres. It has the same function, but it’s much easier to clean and keep sanitized. It’s a good solution for the food and beverage industry, as well as the medical and pharmaceutical industries.”
We published a comprehensive Buyer's Guide.
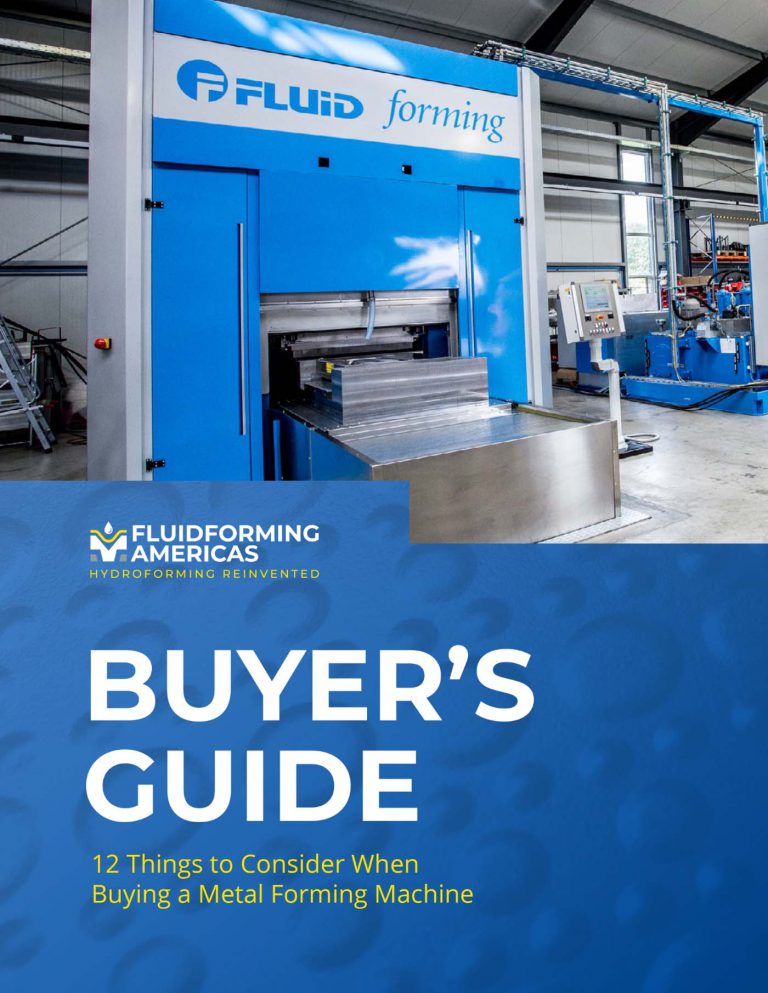
Our fingers were just busy pressing keys as the FormBalancer was pressing precision parts for our customers.
Our Buyer’s Guide helps business owners make an informed decision about which metal forming process — and press — is right for their shop.
We went to FABTECH and it was fab.
Showcasing complex parts formed by our FormBalancer presses, we had the opportunity to explain our process, technology, and services to hundreds of North American manufacturers and innovators. It was grand.
We built a better mousetrap.
Well, we metal formed a better tank end head, created the prototypes for an award-winning hand rinsing device, formed lighter parts for an airplane engine, and formed a flawless heat exchanger for innovative solar panels.
We expanded our services.
It’s official: FluidForming Americas is your one-stop shop for FluidForming hydroforming, sheet metal forming, tube forming, project management, rapid prototyping, finite element analysis, and more. Visit our new-and-improved services pages to learn more.
Green machines, good for manufacturing.
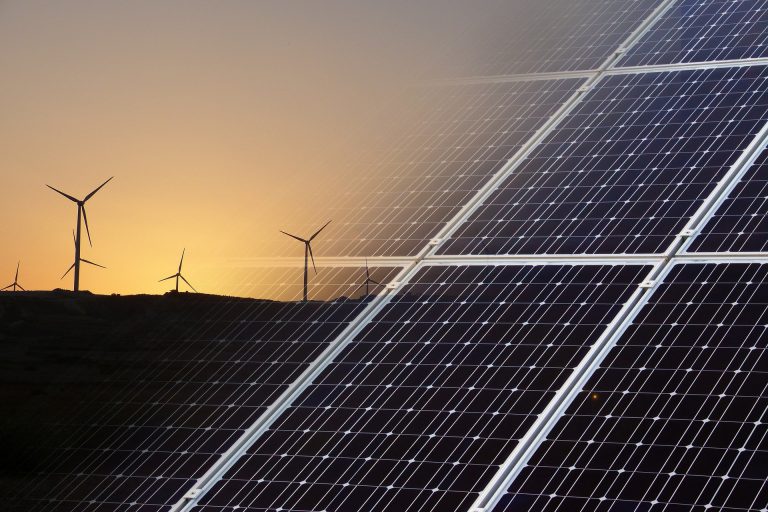
Green manufacturing is a big deal that’s getting even bigger. Green manufacturing happens when companies change business and manufacturing practices — and the mindset of its employees and customers — to mitigate the industrial impact on climate change and other environmental concerns.
We’re ready to help. FluidForming — and FluidForming Americas — helps make green manufacturing possible for product developers, innovators, and manufacturers across the country. Our inherently green manufacturing process is better for the American economy and the environment; and it makes great business sense, too. Visit our blog to learn more.
The R&D tax credit.
In case you haven’t heard about it yet, the research and development tax credit is a huge deal for manufacturers. The R&D Tax credit is one of the easiest ways for American manufacturers to significantly reduce their income liabilities . . . while improving their products and processes.
Here’s a four-part test to help you determine whether or not your business qualifies for the research & development tax credit:
- Permitted purpose: The activity must be related to developing or improving the functionality, quality, reliability, or performance of a business component (i.e. product, process, software, technique, formula, or invention).
- Technological in nature: The business component’s development must be based on a hard science, such as engineering, physics and chemistry, or the life, biological or computer sciences.
- Elimination of uncertainty: From the outset, the organization must have faced technological uncertainty when designing or developing the business component.
- Process of experimentation: The company must have evaluated multiple design alternatives or employed a systematic trial and error approach to overcome the technological uncertainties. (i.e. prototyping.)
If you need new metal forming equipment and you’d like to take advantage of massive tax benefits, talk to your tax advisors and then give us a call.
You like us. You really, really like us.
We couldn’t have done it without you. Thanks to your engagement and support, we have over 1,000 followers on LinkedIn. If you haven’t already joined our fan club, please do. We’d like to return the favor! And if you just want to see us in action, head on over to our YouTube channel and subscribe.
Let’s make some great metal forming moments in 2022! To learn more about our FluidForming hydroforming, project management, or prototyping services, or to learn more about buying a FormBalancer metal forming machine for your facility, contact FluidForming Americas at (800) 497-3545 or email us at info@ffamericas.com.
FluidForming Americas, Inc. is a member of the Precision Metal Forming Association and is AS9100 Rev D, ISO 9001:2015 certified.