Types of metal forming presses: mechanical vs. hydraulic vs. fluidforming
Let’s break it down into three types of metal forming presses: traditional mechanical presses, traditional hydraulic presses, and bladderless hydroforming presses.
Mechanical Stamping Presses
If you’re looking for speed — and you’re willing to sacrifice accuracy, precision, repeatability, finish quality, and sustainability — traditional mechanical stamping presses achieve the highest production volume of simple, shallow-formed parts. With fixed stroke lengths, mechanical presses are less adjustable and rely on progressive dies, which are very costly.
Bladder-based Hydraulic Hydroforming
Legacy hydraulic presses were widely adopted in the 1950s. They can’t achieve the high cycling speeds of mechanical presses, but they’re more variable and perform better with complex shapes and geometries. Bladders used in a traditional hydraulic hydroforming press limit forming pressures to approximately 10,000 psi. Bladders are also prone to failure and can limit precision, repeatability, and may even leave friction marks, damaging the finish of the final product. Non-conforming part waste, consumables, and post-production fixturing should be factored into the relatively low initial cost of these machines.
FluidForming Hydroforming
The new process was quickly and widely adopted in Europe upon its introduction in the early 2000s. Today, companies like BMW, Miele, and Porsche all rely on the process for their high-quality products.
Established in the United States in 2014, the technology has been slower to take off, but companies are slowly starting to experiment with the process and are discovering its incredible capabilities.
Bladderless deep draw hydroforming presses, like FluidForming’s FormBalancer presses, eliminate costly, rupture-prone bladders and environmentally harmful hydraulic fluid. These presses achieve forming pressures of up to 60,000 psi, resulting in 99.996% accuracy and repeatability. Low tooling, operation, maintenance, and post-production costs and minimal material waste ultimately offset the higher initial cost of the technology.
For more information on metal forming presses, download our free Buyer’s Guide.
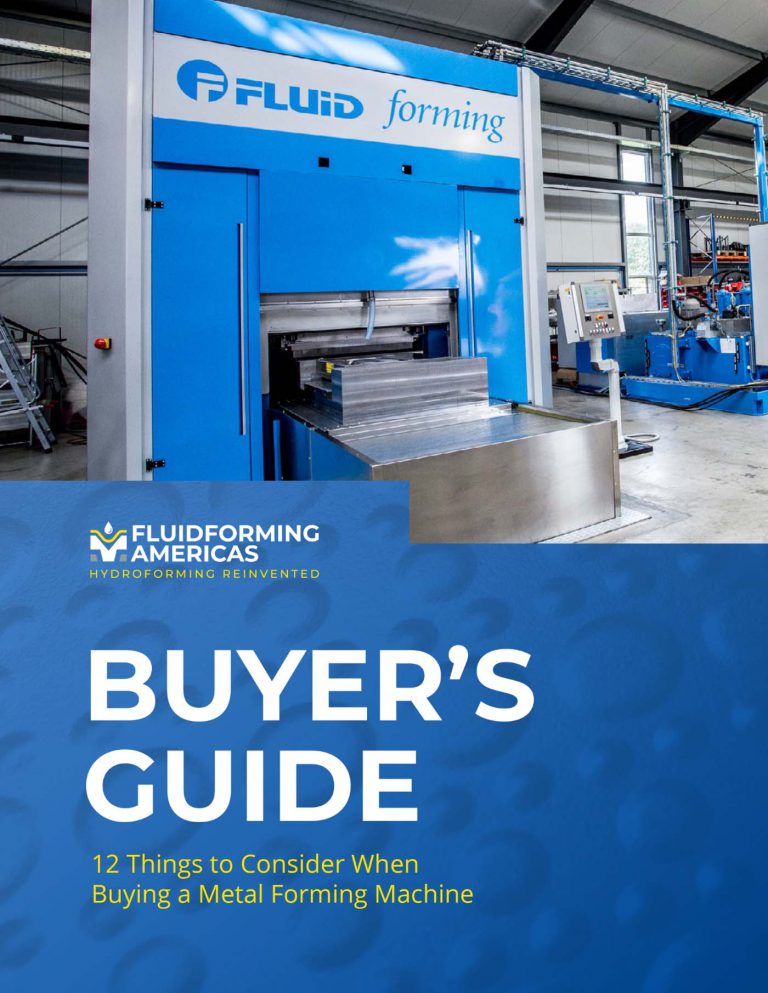
A brief history of hydraulic hydroforming
Let’s take a quick step back and look at hydroforming’s long and storied history. As far back as the 1950s, companies realized the benefits of hydroforming. Rolling on the wave of industrial innovation and futuristic thinking, manufacturers quickly found their preferred presses and processes. Invested in them. Invested in more of them. Repaired them. Modified them. Stuck with them.
And then they stuck with them some more . . . all the way into the next century! Can you imagine computing technology lasting that long? The golden age of automotive manufacturing and American industrial workers was also the peak of hydroforming innovation. It also means that for many, American metal forming is stuck in the 1950s.
It’s time to get unstuck. There’s a new entry into the “types of metal forming presses” category: FluidForming FormBalancers. FluidForming is a reinvention of hydroforming that makes good, clean sense for the 21st century. Thanks to generous federal research & development tax credits, companies can finally replace aging hydroforming equipment with new presses and new technologies — like FluidForming FormBalancer presses. When compared to legacy metal forming processes, FluidForming is an environmentally friendly, sustainable metal forming process.
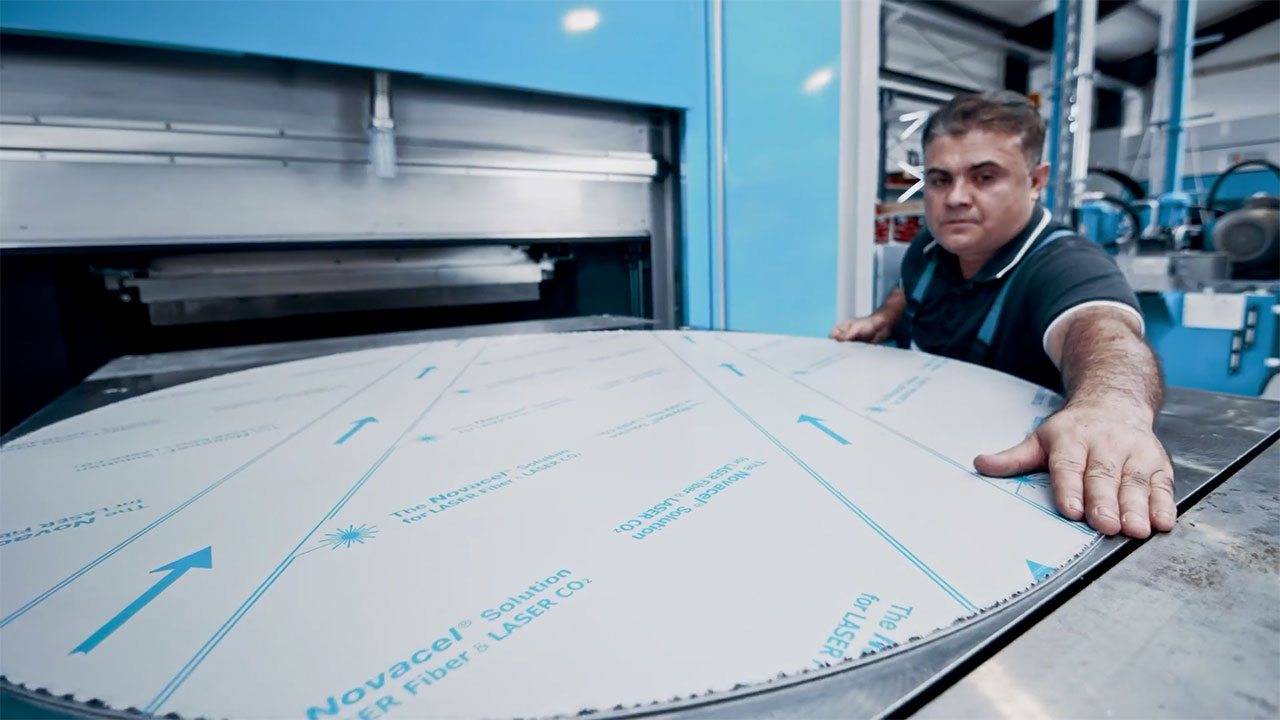
New hydroforming technology for modern times
As the need for lighter-weight products that are both durable and performance-minded increases, manufacturers need a metal forming process that can keep up with their increasingly demanding needs. Not only that, but environmentally-minded manufacturers need processes that are environmentally sound and sustainable. Not only is sustainability a big deal for manufacturers, but it’s also a big deal for consumers — especially younger consumers — as well.
“Time and time again, we’ve had conversations with product developers and engineers who see the potential of our metal forming process. They can clearly grasp the quality and performance benefits and they can see the big-picture savings opportunities that the process offers. The challenge for us is helping CEOs and CFOs understand the cumulative savings opportunities and quality benefits of FluidForming,” notes FluidForming CEO Paul Benny.
FluidForming — which is inspired by legacy hydroforming — reaches higher levels of accuracy and repeatability and offers manufacturers a new way to bring better products to market more quickly, cost-effectively, and sustainably.
The hardest part? Making the leap from legacy hydroforming, with its long and storied history and solid track record, to a relatively new technology. European markets have fully embraced the technology, grasping the big-picture benefits and cost savings. Unfortunately, taking this kind of technological leap is a non-starter for many American companies.
Here at FluidForming America’s, we’d argue that this conservative approach to manufacturing is short-sighted.
“Often, line items — like tooling and post-production fixturing, for example — come from entirely different budgets. Which means the big picture savings and quality advantages disappear behind a screen of incomplete dollar signs,” says Benny. “So although the cost of our process — at first glance — is higher than conventional stamping, FluidForming’s tooling, material waste, non-conforming part waste, and post-production fixturing, are all significantly lower than legacy metal forming methods. And when you factor in tax credits for research and development. It should be an easy argument to win. Unfortunately, the general resistance to change coupled with siloed budgeting processes has been a challenge for us.”
To learn more about FluidForming or our FormBalancer metal forming presses, contact FluidForming Americas at (800) 497-3545 or email us at info@ffamericas.com.
FluidForming Americas, Inc. is a member of the Precision Metal Forming Association and is AS9100 Rev D, ISO 9001:2015 certified.